Top 5 Essential Steps to Avoid Protective Coating Problems on Oil & Gas Assets
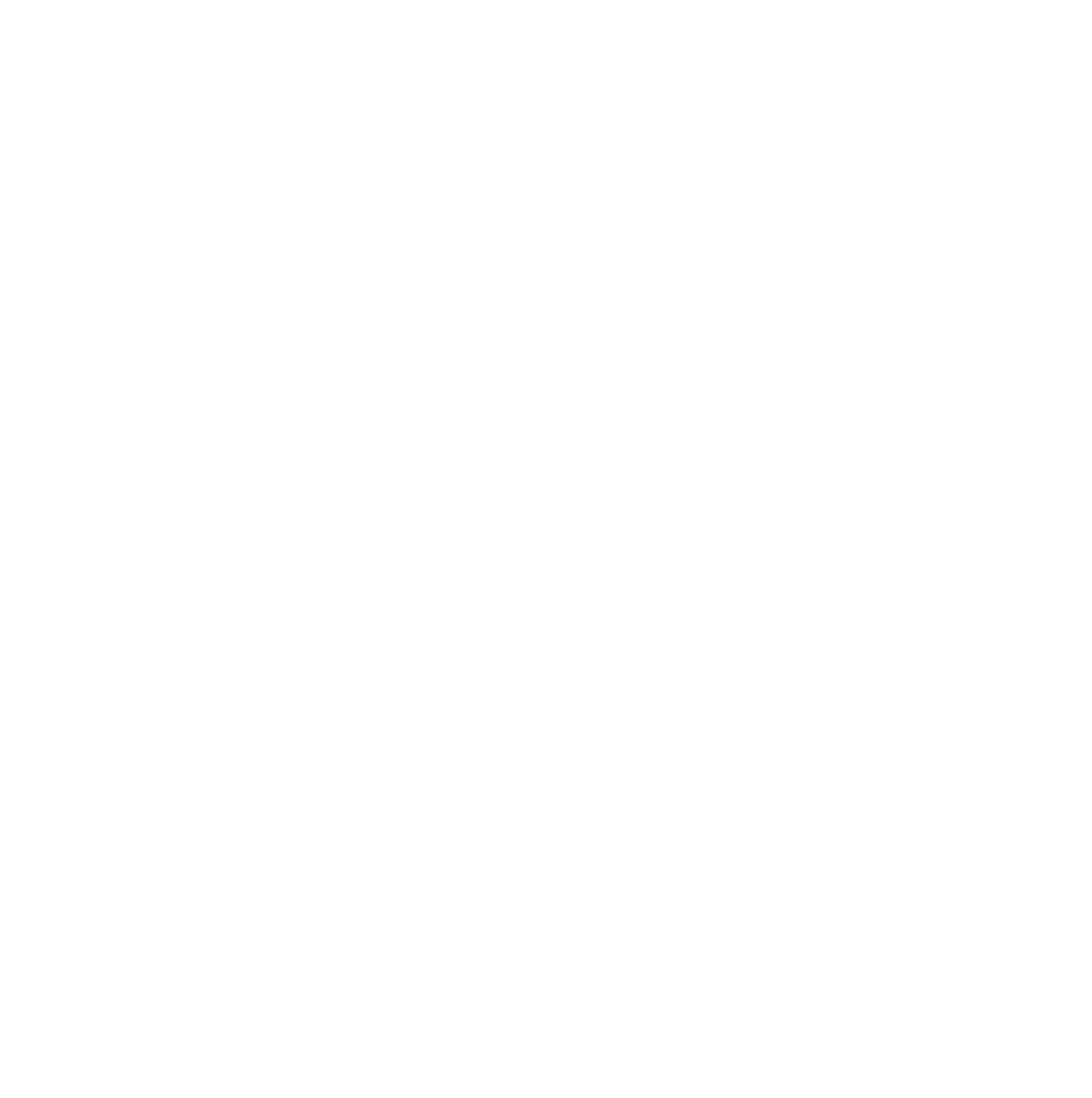
By ExcelPlas Coating Consultants
Ensuring Tight Specifications
Specifications protect both the Owner and Contractor with a course of action agreed by all for best outcome. International recommends that a specification is written detailing surface preparation, coating application and post inspection(s).Finding skilled contractors who have worked in the industrial sector performing abrasive blasting and application is important towards ensuring that your specifications and maintenance are appropriate yielding optimal results.
Choosing a Thin Film or Thick Film
New steel and existing steel with no or minimal corrosion pitting is generally lined with a thin film, one or two coat epoxy scheme. Steel substrates with moderate to heavy corrosion may require thicker films.
Applying Cleaning and Abrasive Blast Cleaning Standards
There are two generally accepted global standards: National Association of Corrosion Engineers (NACE) – Society for Protective Coatings (SSPC) joint standards and International Standards Organization (ISO) 8501 Although the NACE-SSPC & ISO grades of cleanliness are thought to be compatible, for simplicity we will utilize SSPC-SP Standards in this module.Prior to abrading the surface, the substrate needs to be cleaned of oil, grease and visible contamination per SSPC-SP.For immersion service, abrasion blast cleaning is usually recommended per SSPC-SP 5 or SSPC-SP 10 achieving a dense sharp, angular profile. Elevated temperature immersion service typically calls for a steel cleanliness per SSPCSP 5 and lesser robust immersion service, SSPC-SP 10 is recommended.Atmospheric service typically requires steel cleanliness as recommended per SSPC-SP 6 and for maintenance and repair may involve SSPC-SP 2 & 3 (hand and power tool cleaned).Why is initial cleaning of the steel important?If the steel has contamination left on the substrate when abrasive blasting begins, the blasting can drive the contaminates further into the profile and/or spread them further.The service life of a protective coating is strongly dependent on the level of cleaning and preparation, NACE quotes “75% of all premature coating failures are caused either completely or in part by inadequate or improper surface preparation”.Sand blasting and application equipment should always be kept in good working order. Important abrasive media and compressed air should also be kept clean of contamination, oil and water.After the substrate has been abraded, care should be given to maintain the properly prepared surface in accordance with the specification of the manufacturer’s Data Sheet and Application Guidelines, until it is ready for application. This could involve dehumidification equipment to keep the abraded steel from oxidising or priming the surface in a timely fashion before the substrate has been compromised. Also, it is important to wear clean boots or booties so as not to track in contamination. Also, keep sweat perspiration from contaminating the surface.Airless application equipment should be in good working condition to include appropriate size air motor(s), fluid section(s), hoses and paint line.
Spray Application of High-Performance, High Solids Coating Systems
Heated plural equipment is generally the most efficient way to spray most high solids, fast cure, epoxy systems The set up for single leg airless application should have a gravity fed hopper assembly and may need an in-line heater and insulated paint hose to maintain higher temperatures for successful spray-out, depending on the product applied.
Comprehensive Post Application Coating Inspection
Post application coating inspection involves:
- Visual inspection – looking for anomalies, runs, sags, bare locations, etc.
- Dry film thickness measuring – to insure it’s within specification and/or manufacturer’s recommendation. A good Standard for measuring dry film is SSPC-PA 2
- Testing the cured film for holidays or pin holes per NACE SP0188-2006 Discontinuity (Holiday) Testing of New Protective Coatings on Conductive Substrates.
- Testing the cured coating for degree of cure by double solvent rub, hardness probe and/or residual exotherm by DSC analysis
Through all these steps in steel preparation and application, there is potential for a disastrous coating failure outcome, if it is not managed appropriately.As discussed earlier, it begins with cleaning the substrate and removing all grease, oil, dust, dirt and visual contamination per SSPC-SP 1.
Another possible contamination to look for, particularly in immersion service at elevated temperatures, are soluble salts; chlorides, sulphates & nitrates, chlorides being most common of the three.Using clean compressed air and abrasive media is important when performing abrasive grit blasting, otherwise contamination is introduced into the blast stream onto the substrate compromising the lining system over a short period of time.
You’ll need to remove all spent blast media and ensure the substrate is dust free, readying the surface for lining application. be sure precautions are taken not to reintroduce contamination, i.e., tracking in dust and dirt on your boots, clothes, equipment, paint hoses/lines, fingers (oil/salt) touching the fresh abraded surface or perspiration introduced to the substrate.Regarding airless spray application, clean air is a requirement for powering the equipment. The new air motors we see today are nothing like the older motors, that could withstand moisture and water in the air stream.
The latest generation air motors did away with a lot of the mechanical parts, springs, and now involves small, high-pressure ports, valves, air signal pneumatic control pilot valves, etc. All of these can be compromised with dirty air and are susceptible to shutting down during application.
Self-generating devices that rely on the same air stream, generate DC current to power the computer running advanced plural airless systems, which can also be compromised with dirty air and thereby shutting down the equipment at an inopportune time.For more information please consult the protective coating library and database at: https://www.coatingsnews.com/