Technical Discussion on the Performance of White HDPE Geomembranes
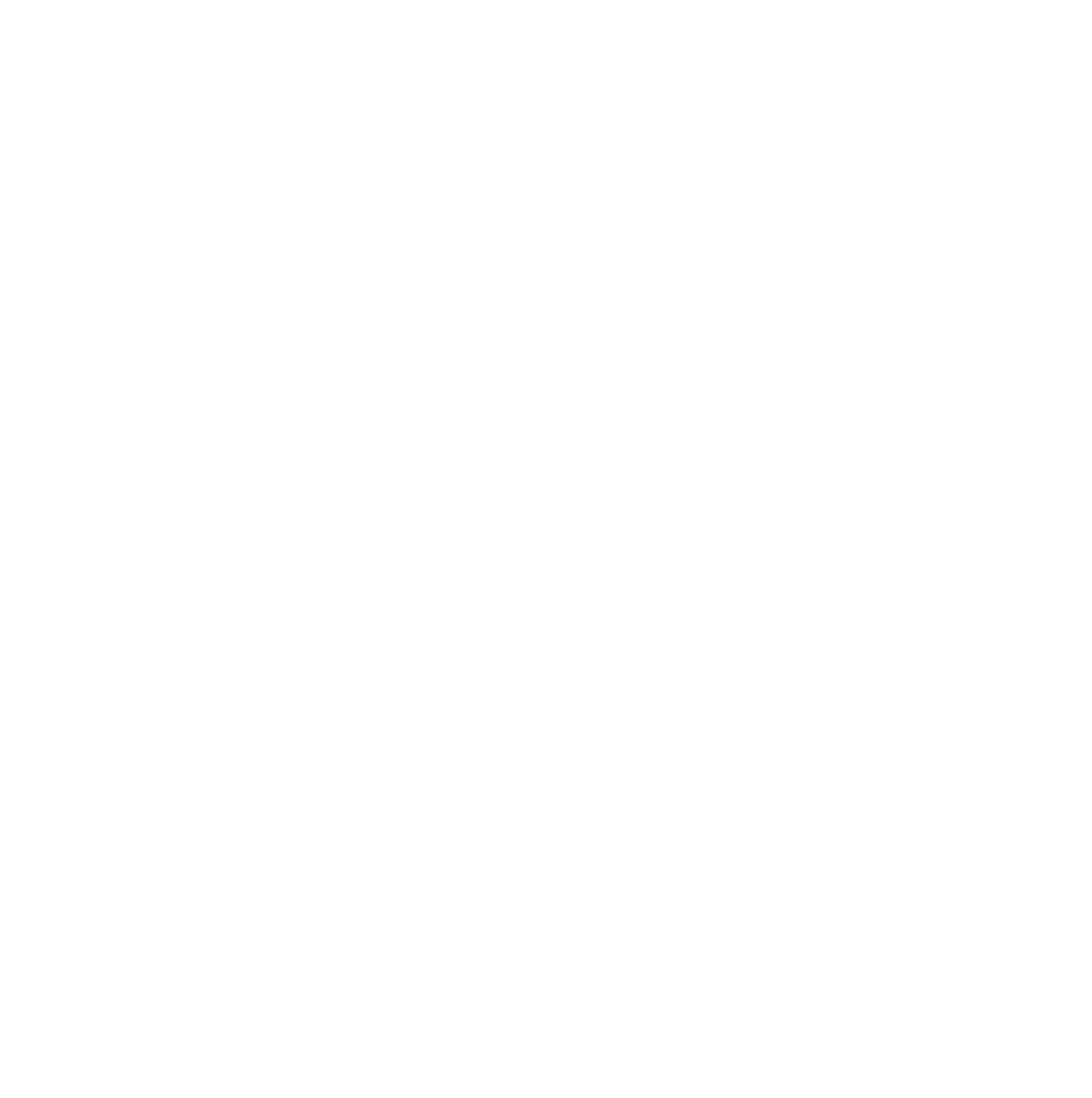
By GNA Editor
Opinion Pieces by Marc Amtsberg (Atarfil) and John Scheirs (ExcelPlas)
Marc has spent 20 years of working in the Geosynthetic sector as both a client and working with major manufacturers and he has observed an ongoing challenge across the industry. Marc has found that remains a general lack of focus on both the Geosynthetic Inputs and Manufacturing Processes that are so critical to product design life.
John has been testing polymers and geosynthetics for 30 years and he has pioneered some of the industry’s latest testing to evaluate long-term durability such as deformulation testing of additives in geosynthetics, thin-film accelerated immersion testing and the use of strain hardening modulus as a surrogate for the NCTL stress cracking resistance test.
An evaluation of the raw material and manufacturing process provide the key insight into expected Geosynthetic performance. Yet this is often overlooked in academic studies, in critical project testing, even for projects that require accountability in EPA regulations.
A reputable manufacturer will have extensive data and must be willing to identify their raw material supplier, their quality processes. If not willing to reveal their polymer inputs, demonstrated testing and project history then serious doubts should be raised over the suitability of their materials.
The fundamental challenge in using Geosynthetics, is short term testing on very small samples is being used to make performance assumptions for projects that can be millions of square metres. This assumption is only correct, if the product properties are replicated across every square metre. A designer who invests time to understand product inputs and manufacturing process, is better equipped to understand this project risk.
In this new GNA series, Marc and John document the most common technical questions encountered for common landfill and mining geosynthetic lining systems. Many of these properties are not measured by QC Testing, but nevertheless are critical in determining Geosynthetic product life.
Introduction
One of the major HDPE Geomembrane industry developments in recent years has seen the growth of “White Top Layer” Geomembranes. The historic benefit has traditionally focused on the white layer’s reduced uptake of heat during exposure, leading to less wrinkles and heat transfer to the subgrade or GCL below. However, there are repeating testing programs and site exhumations that demonstrate White Layers can demonstrate both superior thermal performance, but also perform better in a wide range of chemistry immersions.At the 2022 ACIGS GEOANZ Conference, Boyd Ramsey presented a “Gundle Road Facility” installation from the mid-1980s and a number of other sites with varying service lives and conditions. Boyd’s conclusion was clear, “Exposed White Geomembrane lasts longer than Black Geomembranes”(Ramsey 2022).This statement is not intended to be categoric, it is benchmarking a White Geomembrane to a Black “equivalent”, that has been subjected to the same evaluation in terms of formulation, resin and manufacturing process.In today’s Insight, we will explore some of the considerations that need to be made to ensure the Black vs White comparison can be made, and the limitations that might present.
Carbon Black vs Titanium Dioxide
The MDPE Resin component of a White or Black HDPE Geomembrane remains around 97% of the material, and the same resin source can be used irrespective of colour. The key product difference is the Carbon Black that provides critical UV resistance is replaced by Titanium dioxide in White layers to provide a similar function.Carbon Black also provides key benefits during the manufacturing process, and specifications attempt to quantify the quantity and dispersion in the finished sheet. Titanium Dioxide has a range of natural sources and types that require increased due diligence. There are few references to measure this in industry, and the challenge is exacerbated by the fact that Titanium Dioxide requires additional formulation additives in the form of surface treatments to achieve the same levels of stabilisation.The key takeaway is that there are a wide range of Titanium Dioxide Grades and the most durable rutile sources are most preferred and specified (see ExcelPlas Technical Note EP-50). It is important to know the Titanium Dioxide grade, but also evaluate the quantities and types of additional stabilisers that ensure desired Geomembrane longevity. This can be achieved by evaluating using Deformulation methods describe in previous “Insights” in this series.
Immersions and Chemical Performance
The added benefits in getting the White formulation correct, are being observed in superior performance when subjected to immersions in certain ranges of chemistry. This has been particularly evident in Brines and High pH conditions that are both well documented as shortening the design life of standard black GRI-GM13 products.The theory is that in contact with certain chemical constituents, the additives that promote increased Titanium Oxide stabilisation and accompanying UV resistance, are also serving a function linked to chemical resistance.
Temperature Performance
The benefit of less heat absorbance in White layers in high daytime temperatures and diurnal variations is also becoming well documented. Observations initially carried out by Cadwallader et al (1993) observed a reduction of 24⁰C in the White Geomembrane surface in clear skies at an ambient temperature of 30⁰C. Evaluations are also showing that in specific White Geomembrane configurations, the temperatures below the HDPE can be reduced to near ambient temperatures, providing significant benefits in terms of reducing subgrade clay desiccation and removing conditions that cause GCL erosion. Furthermore lower material temperature reduce the heat history of the HDPE geomembrane hence preserving the reservoir of stabilizing additives.The increased use of drones is also becoming a common method to demonstrate both lower wrinkle heights at ground level but also less wrinkle connectivity from above. Both are properties of wrinkle propagation that limit Geomembrane liner performance.
Conclusions
The original function of White Geomembranes was to encourage reduced heat effects that cause wrinkling and wrinkle connectivity onsite. This is being confirmed by site analyses.The exhumations of White Geomembranes that have been exposed on slopes and within the tidal zones of critical pond containments for in excess of 30 years, is also demonstrating properties that outperform their Black equivalents.This is a function specific to the White Formulations used, that can observe lower temperatures and reduced oxidation rates through the liner thickness, but also provide higher resistance to specific chemistry types. These factors combined are the key measures that determine HDPE Geomembrane longevity, White Geomembranes with the right formulation, will perform better than Black Geomembranes, with added benefits to improve performance of the subgrade Clay or GCL below.
Key Takeaway
White Geomembrane performance is showing superior performance in certain chemistry types, improved thermal benefit and markedly longer design life.This is only assured however, if the grade of Titanium Dioxide is carefully considered, and it is linked to an understanding of the formulation constituents.
Conclusions
In the realm of geomembranes, ensuring reliable and durable performance demands a multidimensional approach. By promoting transparency in resin source disclosure and encouraging comprehensive testing techniques, including Deformulation testing and immersion testing, the industry can bridge the gap between laboratory-controlled conditions and real-world challenges. This shift toward openness and meticulous evaluation will empower engineers, asset owners, and manufacturers to collaboratively develop geomembranes that excel in diverse environments and deliver on their promises of longevity and effectiveness.
References
Referenced Material
Cadwallader, Cranston, Peggs (1993) “White-surfaced HDPE Geomembranes: Assessing their significance to liner design and installation”. Geosynthetics ’93, Vancouver Canada.
ExcelPlas Technical Note 50 – “Not all Titanium Oxide White Pigments are Created Equal”. ExcelPlas 2021 (see GNA Newsletter history)Ramsey (2022) – ACIGS – GEOANZ
#1 Presentation “White Polyethylene Geomembrane: It lasts longer”. ACIGS - GEOANZ#1 – Advances in Geosynthetics. Boyd Ramsey Consulting boyd@boydramseyconsulting.com