pH Modifiers and Polymers in Bentonite
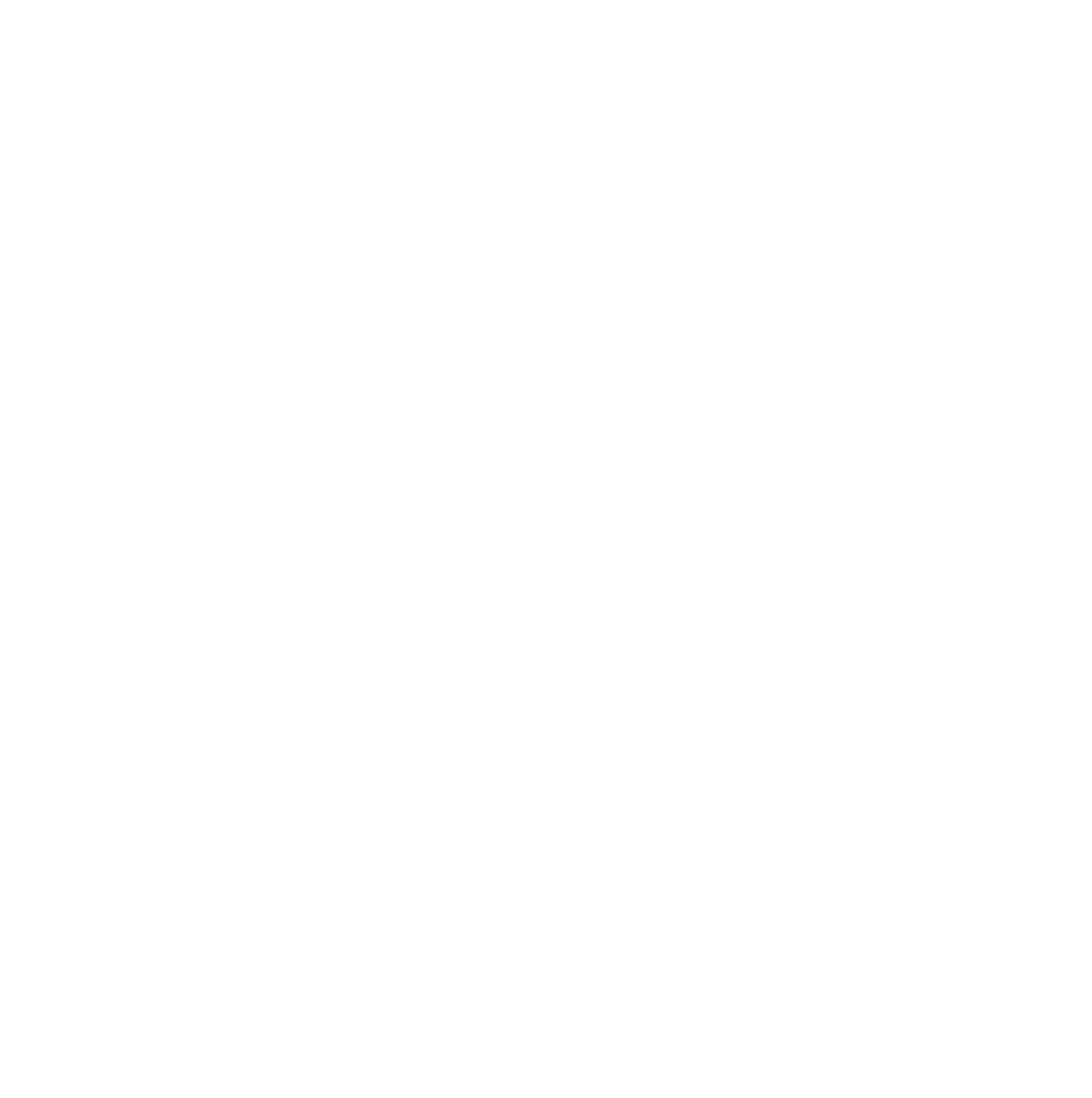
By GNA Editor
Opinion Pieces by Marc Amtsberg (Atarfil) and John Scheirs (ExcelPlas)
Marc has spent 20 years of working in the Geosynthetic sector as both a client and working with major manufacturers and he has observed an ongoing challenge across the industry. Marc has found that remains a general lack of focus on both the Geosynthetic Inputs and Manufacturing Processes that are so critical to product design life.John has been testing polymers and geosynthetics for 30 years and he has pioneered some of the industry’s latest testing to evaluate long-term durability such as deformulation testing of additives in geosynthetics, thin-film accelerated immersion testing and the use of strain hardening modulus as a surrogate for the NCTL stress cracking resistance test.An evaluation of the raw material and manufacturing process provide the key insight into expected Geosynthetic performance. Yet this is often overlooked in academic studies, in critical project testing, even for projects that require accountability in EPA regulations.A reputable manufacturer will have extensive data and must be willing to identify their raw material supplier, their quality processes. If not willing to reveal their polymer inputs, demonstrated testing and project history then serious doubts should be raised over the suitability of their materials.The fundamental challenge in using Geosynthetics, is short term testing on very small samples is being used to make performance assumptions for projects that can be millions of square metres. This assumption is only correct, if the product properties are replicated across every square metre. A designer who invests time to understand product inputs and manufacturing process, is better equipped to understand this project risk.In this new GNA series, Marc and John document the most common technical questions encountered for common landfill and mining geosynthetic lining systems. Many of these properties are not measured by QC Testing, but nevertheless are critical in determining Geosynthetic product life.
pH Modifiers and Polymers in Bentonite
Introduction
The role of Bentonite has been previously defined as the key component of Geosynthetic Clay Liners responsible for hydraulic performance. The importance of raw material source, the need to understand the dominant exchangeable cation (sodium or calcium) and knowing the types/content of certain impurities are critical to the understanding of long-term performance.The ideal Bentonite is Natural Sodium montmorillonite (by dominant Cation and CEC) but there are few commercial sources left in the world. The US remains the primary source, Australia and Turkey have select sources, but the now dominant Chinese and Indian markets mine Calcium Bentonites that require Sodium Activation (SA).It is therefore critically important to understand the role and risk of these additives that are added to the raw material to improve long term performance. Even natural Sodium sources defined by their predominant Sodium Cation are “beneficiated” to increase the percentage of Sodium cations, and meet Australian EPA Regulations.The inherent risk to long-term GCL performance, is the quantity, type and methods used by the GCL supplier to facilitate this process.
pH Modifiers or Polymers
The Australian GCL industry has become focussed on two key categories that summarise these additives;
-pH Modifiers
The most obvious addition to the raw material is ‘soda ash’ activation (sodium carbonate) to increase sodium content and promote increased Swelling and Fluid Loss performance. This is a pH modifier, and added to all GCL Bentonites supplied to Australian specifications.The influence of Soda Activation is unpredictable, “…and a careful evaluation of each deposit should be made.” Odom (1984).Analysis of the GCL’s Bentonite raw material and Soda Ash quantities are critical to understand long term GCL impacts.
-Polymers
There are a vast range of both Anionic and Cationic Polymers added to Bentonites for a range of functions. The Polymer type, quantities and method of addition will vary significantly according to the Bentonite source, and results in marked differences in Bentonite-Polymer interaction and therefore GCL performance.It is extremely difficult to identify and quantify Polymer additions. A desktop evaluation can identify the function of the Polymer, but requires analysis of the Bentonite raw material, the Polymer types and the quantities of addition. The Bentonite mine may be reluctant to release this information, but the Victorian EPA BPEM Guideline has demanded it from the manufacturer since 2010.In lieu of detailed information, long term testing that promotes polymer elution can provide significant expectations as to site performance. This can be in the form of subjecting the GCL to long term immersions, wetting and drying, and site conditions that promote erosion and challenge clay fabric.
Conclusions
The benchmark GCL specifications in Australia require Bentonites that contain additives in the form of pH modifiers and/or polymers, and these have been documented as a potential risk to hydraulic performance.Analysis of the raw Bentonite and the additive types/quantities can provide critical long term prediction, but as per all Geosynthetics, product testing consistency and long term testing remains the key predictor of long term performance.The Victorian EPA “BPEM” Landfill Guideline has highlighted this Bentonite risk since 2010;“…other additives, such as polymers or pH modifiers, may be added to improve the swelling and sealing capability …... If used, the manufacturer should provide their details and demonstrate their nature, suitability and long-term durability.”
Key Take Home Points
- Raw material source, dominant exchangeable cation (sodium or calcium), and impurity types/content are vital for understanding long-term GCL performance;
- Ideal Bentonite is Natural Sodium montmorillonite, but commercial sources are limited globally;
- US, Australia, Turkey have sources; China and India dominate with Calcium Bentonites requiring Sodium Activation (SA);
- Additives improve long-term GCL performance, but their type, quantity, and methods matter;
- 'Soda ash' activation is a pH modifier to enhance sodium content, swelling, and fluid loss performance;
- Soda Activation's influence is unpredictable, demanding evaluation for each deposit;
- Analysis of raw material and soda ash quantities is crucial for GCL impact understanding;
- Polymers, both Anionic and Cationic, are added to Bentonites for various functions;
- Polymer type, quantity, and addition method vary by Bentonite source, impacting GCL performance;
- Identifying and quantifying Polymer additions is challenging; requires analyzing raw material and Polymer information.
References & Further Reading
Gates, W.P., Anderson, J., Raven., M.D., Churchman, G.J. 2002. Mineralogy of a bentonite from Miles,Queensland, and characterisation of its acid-activation products. Applied Clay Science, 20, 189-197.Odom, I.E. 1984. Smectite clay minerals: properties and uses. Philosophical Transactions Royal Society,London A, 311, 391-409.Victorian EPA Landfill “BPEM Guidelines”: 2015