New Naming Convention for ACP Cladding to Catch Out Manufacturers Using Cheap Chalk Fillers and Extenders
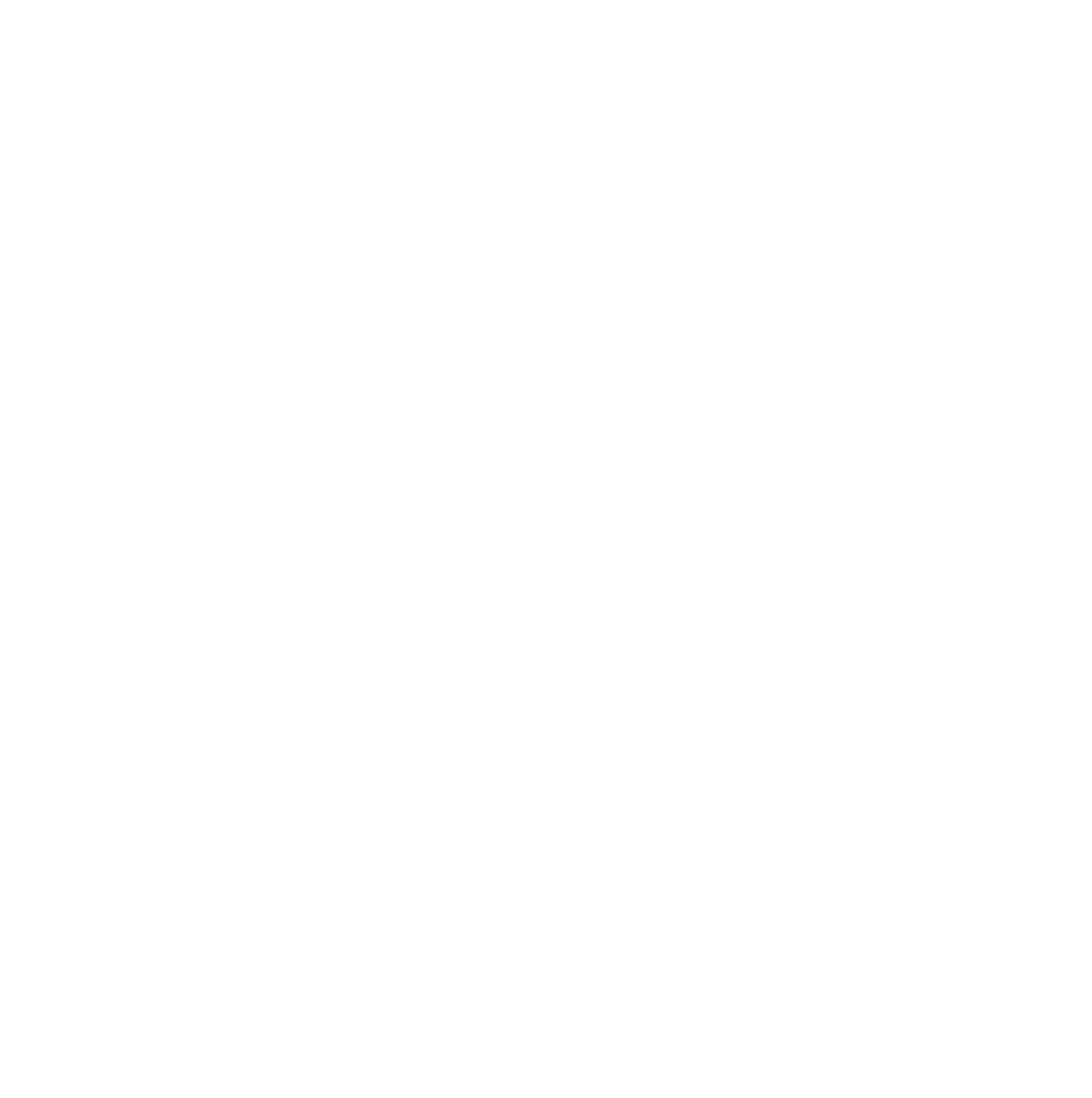
By CCN Editor
Introduction
The use of Aluminium Composite Panels (ACP) in construction has raised significant concerns about fire safety. Some manufacturers have been found to use cheap fillers such as chalk or calcite (types of calcium carbonate) to mislead testing laboratories. These fillers do not provide any flame retardant properties, thus posing a significant fire risk. To address this issue, a new naming convention has been adopted to distinguish between ACP panels based on the presence and proportion of flame retardant (FR) fillers.
New Naming Convention
The new naming convention for ACP panels is designed to capture and highlight the presence of flame retardant materials. For example:
- ACP-FR70: This refers to an ACP panel that contains approximately 70% flame retardant fillers such as Aluminium Trihydroxide (ATH) or Magnesium Dihydroxide (MDH) and hence 30% PE.
- ACP-NFR45: This indicates a panel with approximately 45% non-flame retardant fillers, such as calcium carbonate.
This convention makes it easier to identify and categorize ACP panels based on their fire safety properties as shown in the table below.
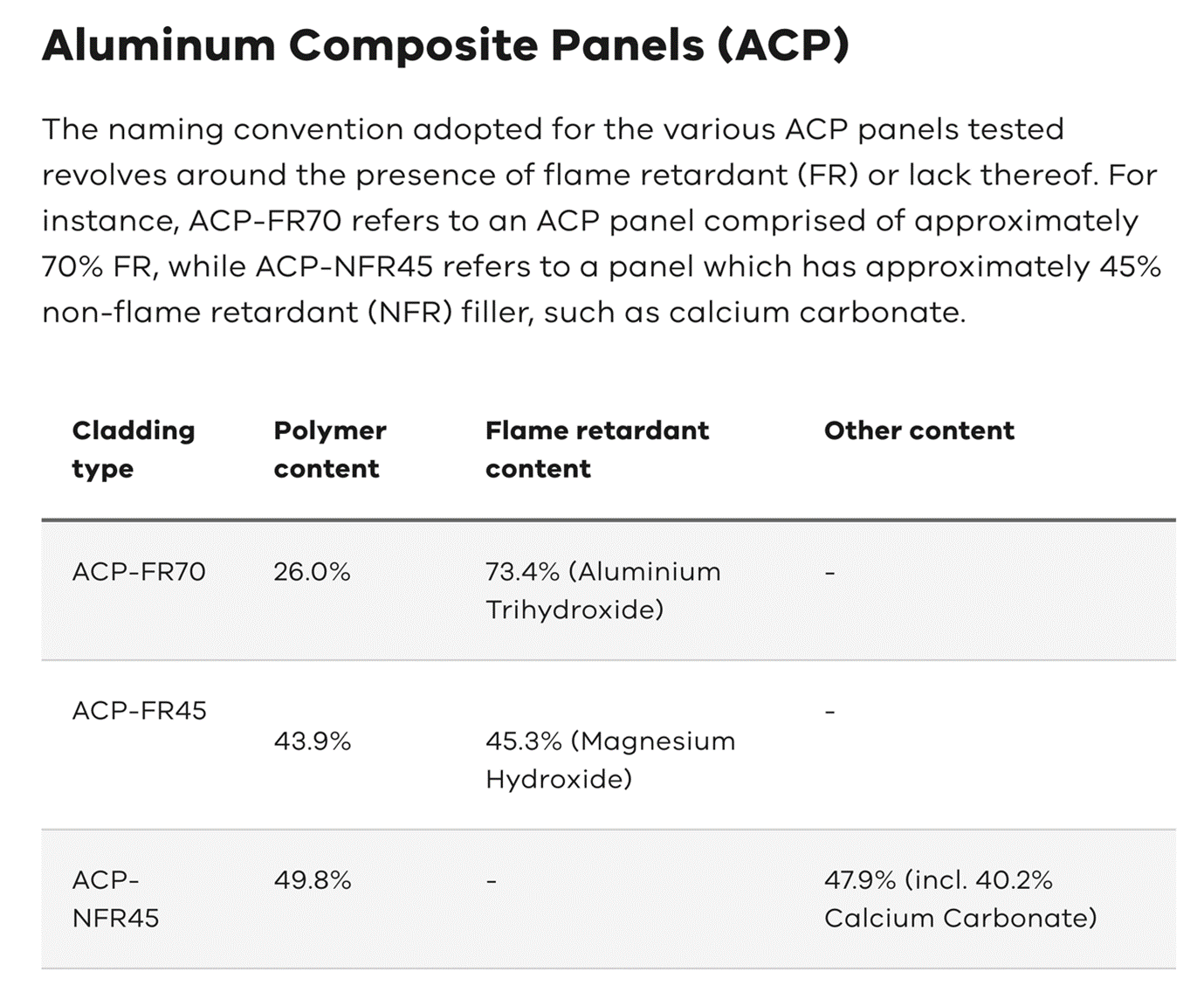
Flame Retardant Fillers
Aluminium Trihydroxide (ATH) and Magnesium Dihydroxide (MDH)
are effective endothermic flame retardants for polyethylene (PE). Their effectiveness is due to several mechanisms:
- Cooling the Flame: Both ATH and MDH decompose endothermically, absorbing heat and thus cooling the flame front.
- Water Vapour Release: During decomposition, they release water vapour, which dilutes the flammable decomposition products of the polymer.
- Formation of Protective Oxides: They form non-combustible refractory oxides on the polymer surface, creating a barrier that protects the underlying material.
The graphic below summarizes the flame retardant properties of ATH and MDH.
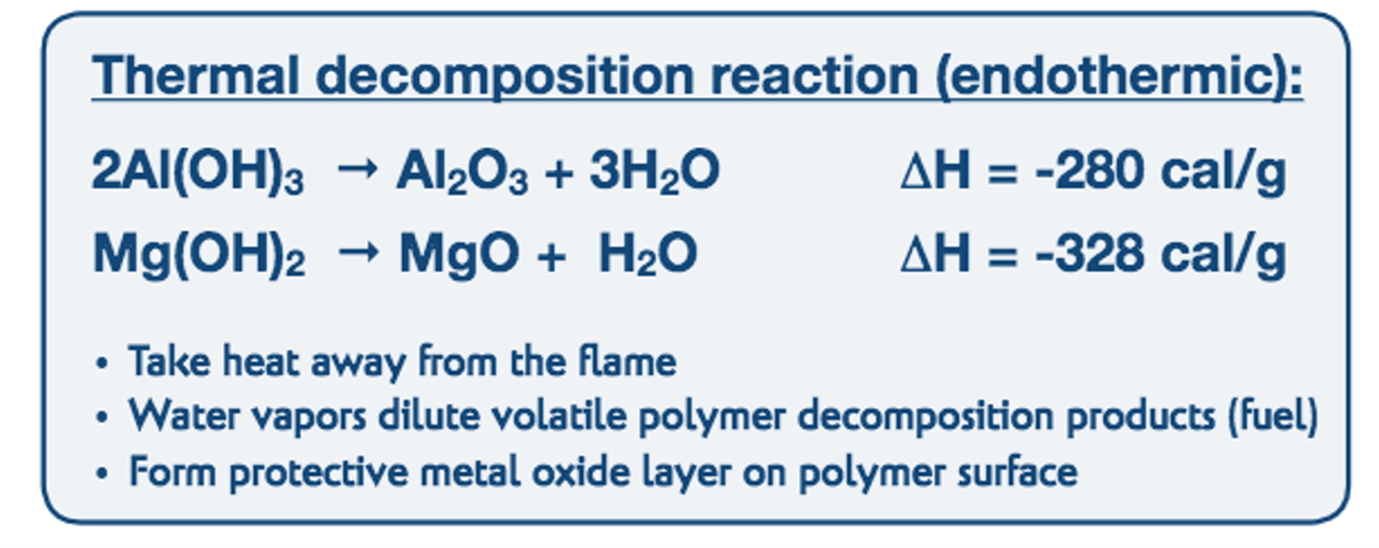
Thermal Decomposition Temperature and TGA Curves
ATH and MDH have different onset temperatures for decomposition, typically around 100°C apart. This difference is crucial for understanding their behaviour in fire scenarios:
- ATH Decomposition: Begins at a lower temperature, providing early flame retardant action.
- MDH Decomposition: Occurs at a higher temperature, offering sustained protection as the temperature rises.
The TGA (Thermogravimetric Analysis) curves below illustrate these decomposition behaviours and highlight their effectiveness as flame retardants.
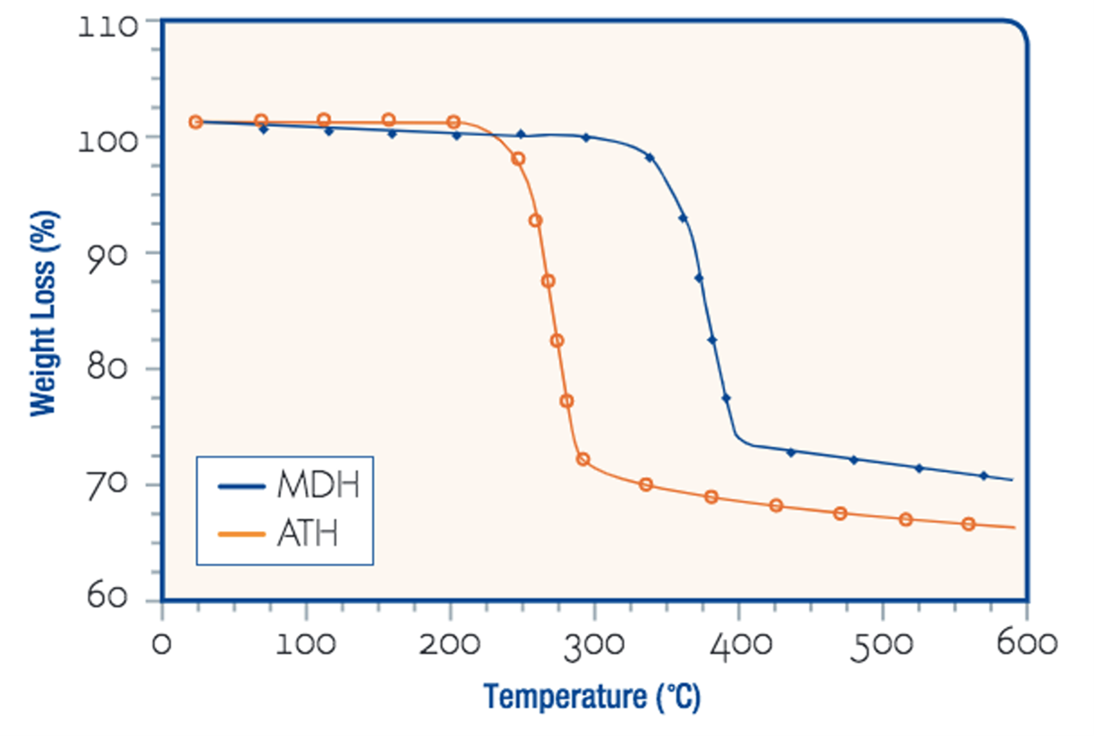
Non-Flame Retardant Fillers
Calcium Carbonate
Calcium carbonate, commonly used as a cheap filler, does not provide any flame retardant properties to PE because there is:
- No Water Vapour Release: Unlike ATH and MDH, calcium carbonate does not release water vapour when heated.
- No Flame Cooling: It does not absorb significant amounts of heat or cool the flame front during combustion.
Misleading Testing Practices
Some manufacturers use calcium carbonate to pass simple ashing tests, which measure the amount of inorganic filler in the PE by burning off the PE. Since calcium carbonate is an inorganic filler, it leaves a high residue in ashing tests, potentially misleading testing labs into thinking the panel contains effective flame retardants.
Advanced Testing Methods
To counteract these misleading practices, ExcelPlas Labs employs advanced testing techniques such as FTIR (Fourier Transform Infrared Spectroscopy) and X-ray diffraction:
- FTIR: Identifies the specific chemical nature of the fillers by analyzing their molecular fingerprints.
- X-ray Diffraction: Provides detailed information on the crystalline structure of the fillers, allowing for precise identification.
These methods ensure that the true nature of the fillers used in ACP products is accurately determined, preventing the use of non-flame retardant fillers from going undetected.
Conclusions
The adoption of a new naming convention for ACP cladding panels is a crucial step in identifying and preventing the use of non-flame retardant fillers. By clearly distinguishing between panels with effective flame retardants and those without, manufacturers, testing labs, and end-users can better assess the fire safety of ACP products. Advanced testing methods like FTIR and X-ray diffraction are essential tools in this effort, ensuring that only safe and compliant materials are used in construction.
To get your cladding tested to best practice industry standards please contact ExcelPlas Labs https://www.excelplas.com/products-tested/cladding-testing/