Rethinking Surface Preparation in Geomembrane Welding: A Critical Comparison with Polyethylene Pipe Fusion
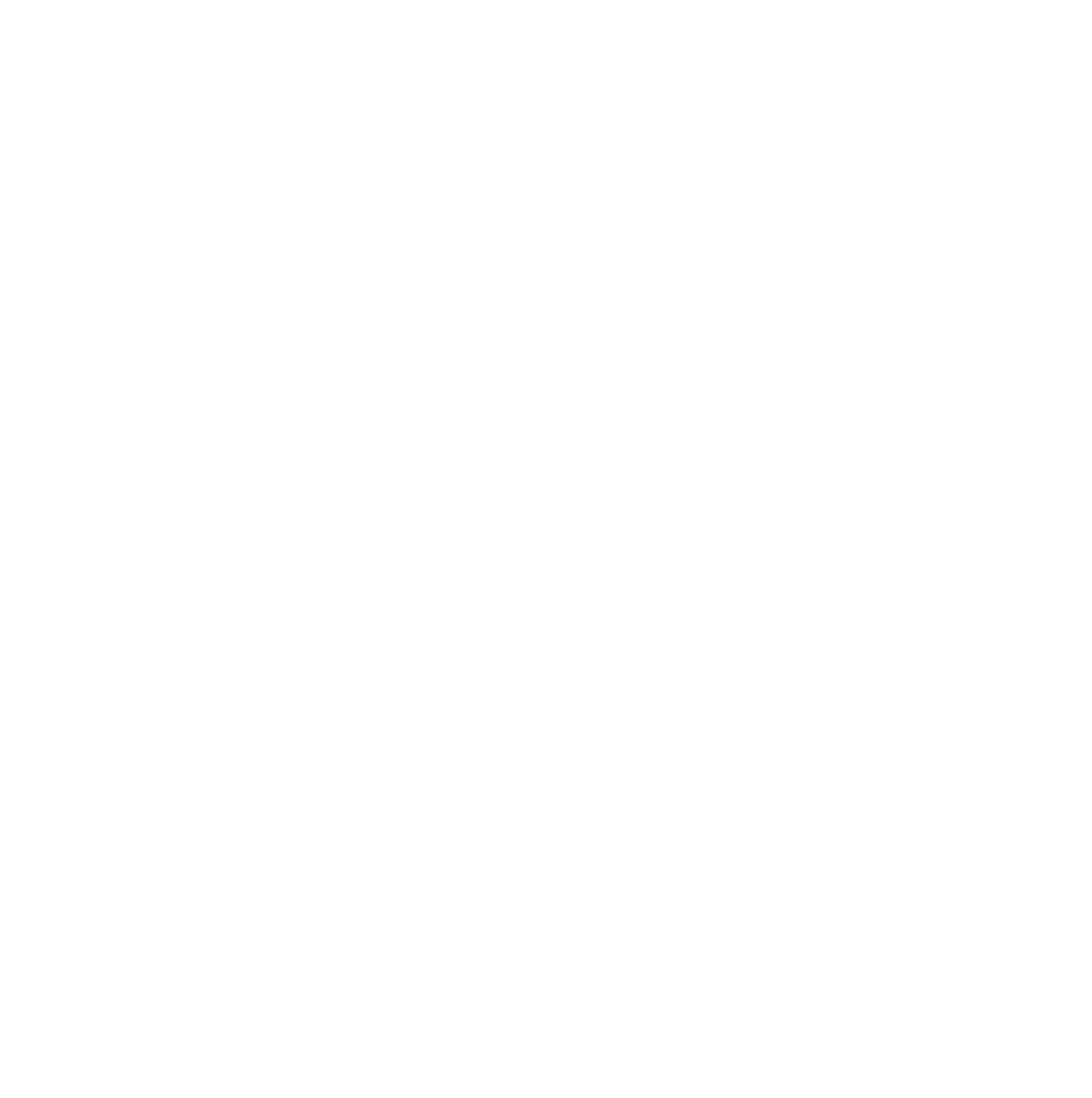
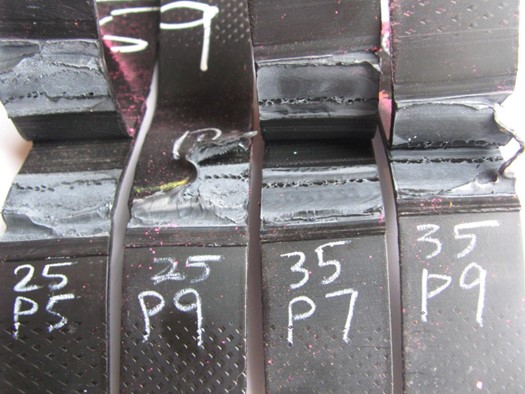
Introduction
In the realm ofthermoplastic welding, surface preparation is a non-negotiable step to ensurelong-term joint integrity. Polyethylene (PE) pipe welding, particularly usingbutt fusion or electrofusion methods,mandates precise facing (or shaving) of the pipe ends.
This practiceremoves the outer surface layer of the polymer, which may contain oxidizedmaterial, waxes, processing additives, or other contaminants that could impairweld quality. The resulting fresh, uncontaminated polymer surfaces fuse effectively under heat and pressure, forminga homogeneous and durable joint.
In starkcontrast, geomembrane welding—particularly the wedge welding of high-density polyethylene (HDPE) or linearlow-density polyethylene (LLDPE) liners—commonly omits any form ofpolymer layer removal prior to fusion.
Instead, surface cleaningis largely limitedto rudimentary techniques: dry cloth
wiping, or theuse of soapy or clean water. Solvent-based cleaning is rarely employed, and mechanical ablation(such as grinding)is typically reservedfor extrusion welding, not wedge or hot air track welding.
The Inconsistency: Surface Chemistry and Weld Quality
This disparity in practice is perplexing when considering the shared material properties between PE pipes and geomembranes. Both are subject to:
- Oxidative degradation from storage and UV exposure
- Additive blooming, wherestabilizers, antioxidants, and processing waxes migrate to the surface
- Surface exudation, especially in co-extruded geomembranes with skin layersenriched in UV or thermal stabilizers
These phenomena create a weak boundary layer on the polymer surface with altered chemical and physical properties. In geomembranes, this layer is often visually apparent as a dull, waxy residue or oily sheen—yet it is not routinely removed before wedge welding. Weld failures in the field, particularly those exhibiting interfacial delamination or poor fusion at the inner weld zone, are increasingly being traced back to these surface contaminants (see image below).
While fusion parameters like temperature, pressure, and speed are rigorously controlled, the cleanliness and initial surface condition of the geomembrane laps remain inadequately addressed. Weld failures such as those shown below are relatively commonplace and can be attributed to surface contamination on the geomembranes, usually in the form of stabilizers, antioxidants, and/or processing waxes, as well as surface oxidation.
The surface of HDPE geomembranes can also be enriched with migratory POSH (Polyolefin Oligomeric Saturated Hydrocarbons) waxes, which are residual low molecular weight hydrocarbons formed in the polymerization of polyolefins (like HDPE and LLDPE). POSH are a mixture of alkanes—typically C20 to C50 fully saturated hydrocarbons (no double bonds) that migrate to the polymer-air interface. They are measured by polyolefin manufacturers using the Cyclohexane Extractables Test (CHE).
It was noted there were porosity tracks and splay patterns on the failed weld surfaces (see photo below) indicating the presence of volatiles and contamination in the weld interface.
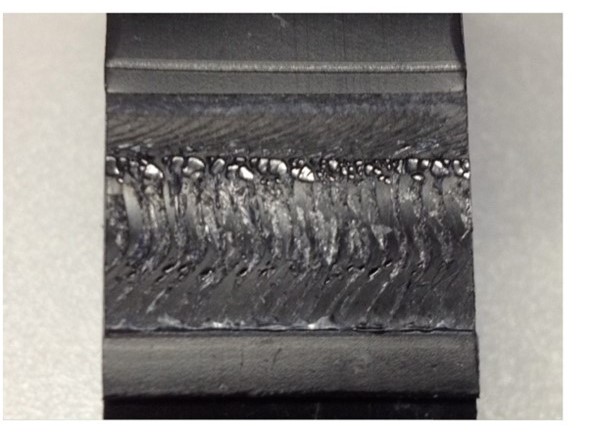
Inadequate Cleaning Methods
The industry’s current reliance on water or soapy solutions is problematic. These polar solvents are poorly suited for dissolving non-polar waxes or low molecular weight additives. As a result, contaminant layers persist through the cleaning process and remain present during welding. Unlike pipe welding, where alcohol wipes (isopropyl alcohol or ethanol) are standard for removing oils and residues, geomembrane welding protocols largely ignore solvent cleaning. This raises the question: why does a high-integrity welding process in pipe systems involve aggressive surface preparation, while geomembrane welding—a similarly critical operation for containment integrity—relies on minimal surface treatment?
A Path Forward: Advanced Cleaning Technologies
To improve the consistency and reliability of geomembrane welding, particularly in critical infrastructure (e.g., landfills, reservoirs, and mining tailings dams), surface cleaning protocols must evolve. Several viable approaches include:
- Solvent Wipes
Application of volatile organic solvents like ethyl acetate, n-heptane, or cyclohexane (with proper safety protocols) can effectively remove waxy blooms and additive residues. Ethyl acetate, in particular, offers a good balance between solvency power and volatility.
- Laser Surface Cleaning
Already employed in rust removal and precision surface decontamination, laser ablation can be adapted for polymer welding. It provides non-contact removal of contaminants without mechanical abrasion, potentially useful in automated welding systems.
- Micro-abrasion or Surface Buffing
Just as extrusion welding of geomembranes involves grinding the sheet prior to polymer deposition, a similar light abrasive process could be introduced before wedge welding. Micro-sanding or non-woven abrasive pads could selectively remove only the contaminated surface layer.
- Plasma Surface Activation
Atmospheric plasma torches, used in automotive and electronics industries, clean and functionalize polymer surfaces without physical abrasion. This method could improve miscibility, wettability, and melt flow during welding. Plasma treatment is cold to the touch and therefore safe to deploy in the field. (see image below).
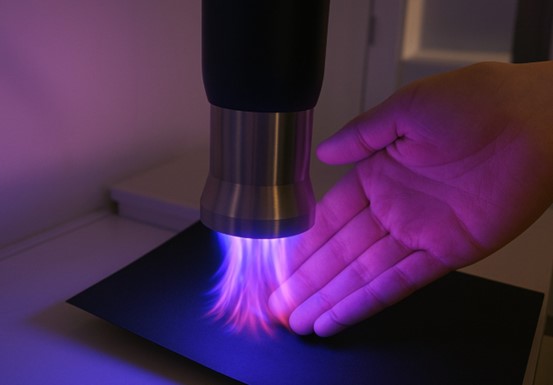
Conclusions
The geomembrane industry must acknowledge and address the inconsistency in surface preparation standards compared to PE pipe welding. As weld failures due to surface contamination become more evident, upgrading cleaning protocols from mere wet wiping to chemical or physical surface treatment is both logical and necessary.
Adopting solvent wipes, laser/plasma cleaning, or abrasive methods will align geomembrane welding practices with established thermoplastic fusion technologies, ultimately enhancing liner integrity, reducing rework, and extending service life in critical containment systems.
While improving surface cleaning methods is a logical step toward reducing contamination-related weld failures, it is equally important to monitor and record the welding conditions under which these interfaces are joined. The integration of data capture systems—logging parameters like temperature, pressure, and speed—provides a crucial audit trail. When paired with improved surface preparation, this technology allows for more accurate root cause analysis of weld failures, distinguishing whether the issue stems from surface condition or parameter deviation. It’s a small but essential step toward a more forensic, performance-driven approach to geomembrane welding.
Get your welds tested now!
Discover ExcelPlas's geomembrane expertise and ensure enhanced containment integrity and extended service life, reducing weld failures and maintenance costs. Get in contact with us today!