Failure Analysis of Polycarbonate Inspection Cover
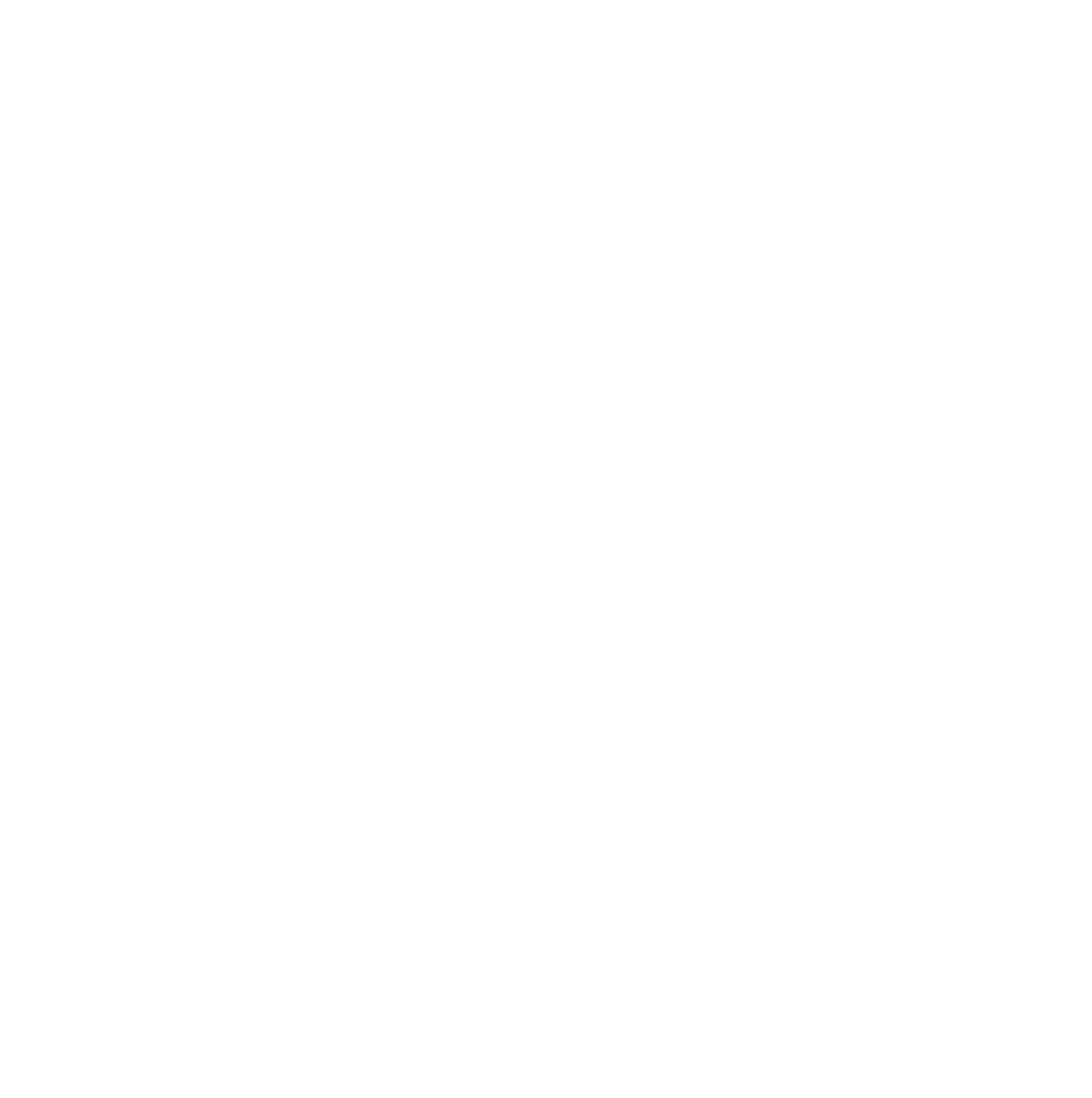
Objective
To investigate the cause of cracking on a polycarbonate inspection cover used in a stainless steel beer tank.
Testing Undertaken
- Stereomicroscopy
- FTIR
To investigate the cause of cracking on a polycarbonate inspection cover used in a stainless steel beer tank. Excelplas polymer testing Laboratories undertook testing methods such as Stereomicroscopy, FTIR Analysis, and ESC Testing in order to understand the nature and failure type of the crack. As part of the background investigation it was found that PUR-SAN-555N was used as a sanitising agent around the manhole cover.
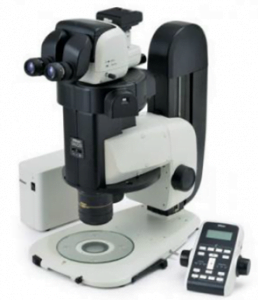
Stereomicroscopy (Microcracking)
Microcracking on dead fold was assessed using a Nikon SMZ25 stereographic optical microscopy (SOM). Only the exposed side of the samples was subjected to 180 degree ‘dead fold’ and was observed for incipient microcracking at various magnifications.The liner samples were bent back and dead folded (180 degrees) so that the surface of the liner was placed in tension and under strain. The bend back specimens were then placed in restraint clips and the top faces of the fold specimens were microscopically examined for any evidence of microcracking.
Whilst the bending stress is somewhat in excess of that likely to be encountered in service it will determine if any incipient micro cracking or brittle layers are present on the liner surface. Quality virgin liner samples subjected to this test do not exhibit any micro cracking.
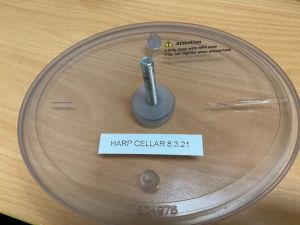
FTIR Analysis
Fourier Transform Infrared (FT-IR) spectroscopy was used for ‘finger-printing’ for material identification of the polymer and filler components. The FT-IR analysis was performed according to ASTM E573 ‘Standard Practices for Internal Reflection Spectroscopy” using an Alpha Measurement Module by Bruker Optik see figure 2. Smaller samples of the core were cut from the larger sample. Spectra of the core were searched against an internal library database for identification.
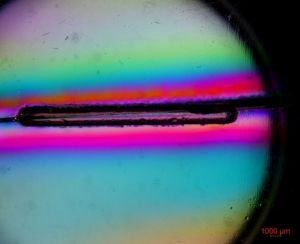
The cracking on the polycarbonate manhole cover was from exposure to PUR-SAN 555N sanitising agent (containing >60% ethanol), which has caused Environmental Stress Cracking on the polymer at the stressed guidelines.
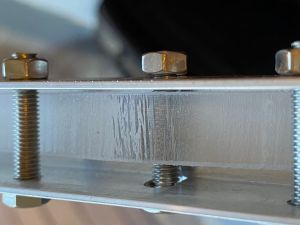