Flat Spots vs. Ovality: What’s Sabotaging Your EF Welds?
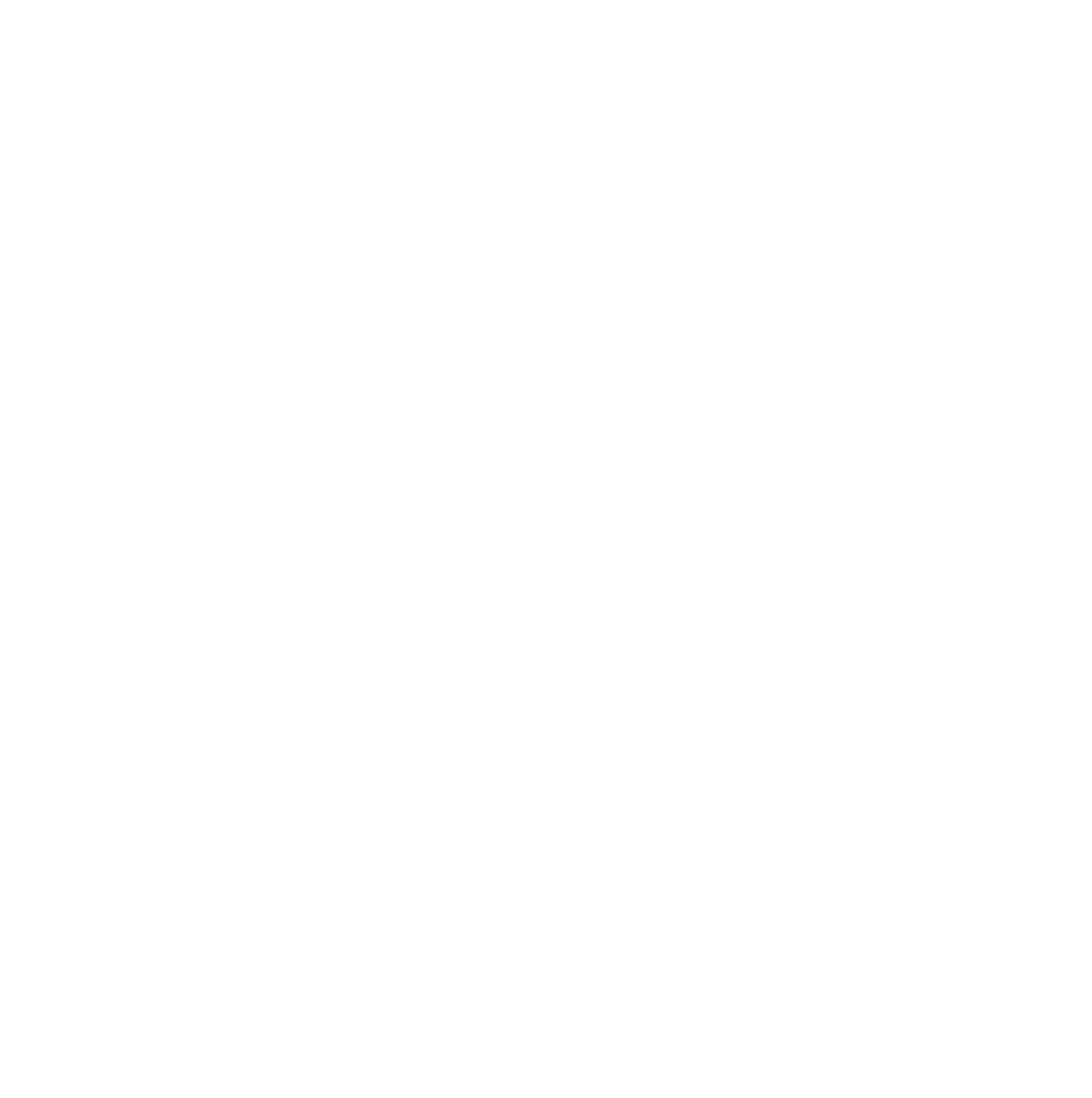
By PPN Editor
When it comes to Electrofusion (EF) welding of HDPE pipes, ensuring the integrity of the weld is paramount. Two common issues that compromise EF welds are flat spots and ovality. While they may seem similar, their causes and impacts differ significantly, and understanding these distinctions is crucial for maintaining welding quality and preventing failures.
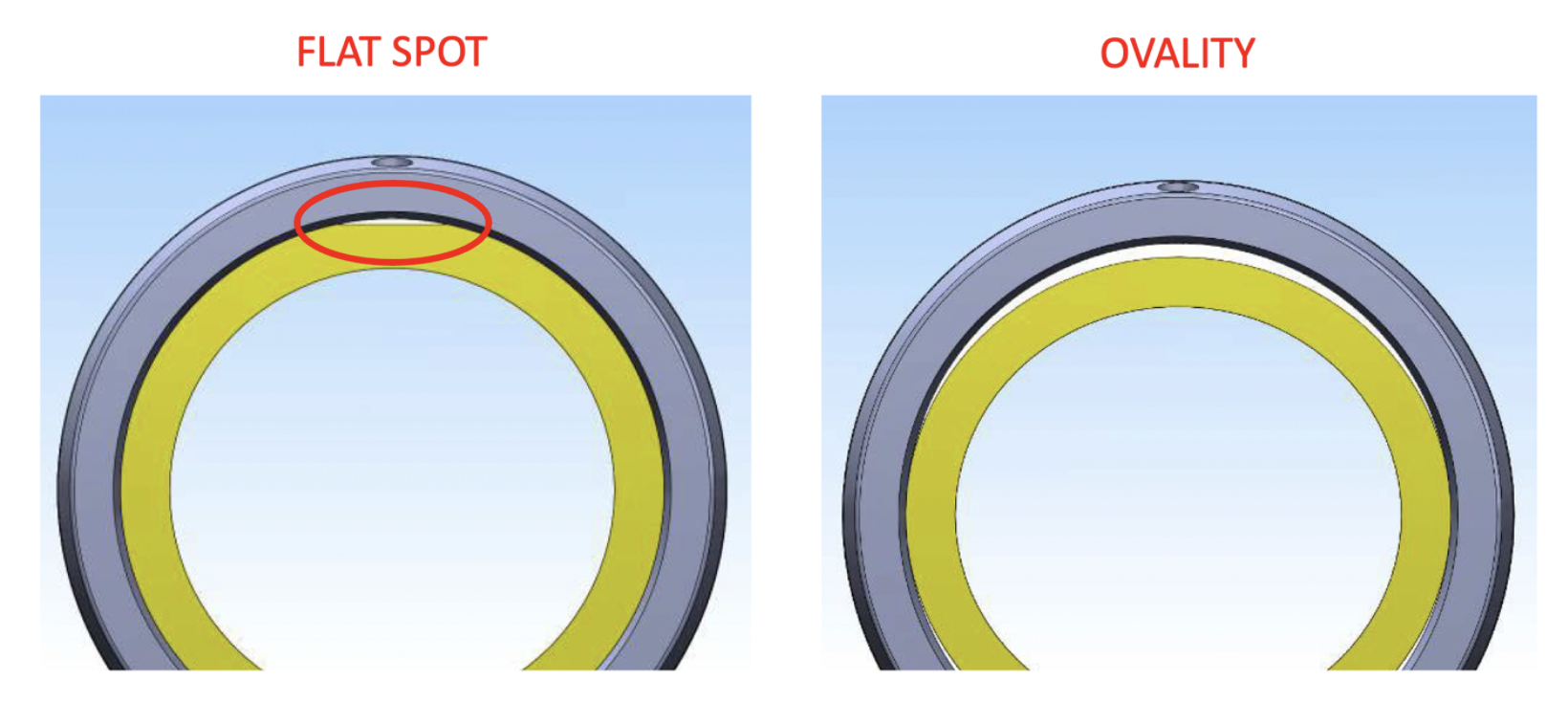
What Is Ovality?
Ovality refers to the out-of-roundness of HDPE pipes. This deformation occurs primarily due to improper transport and storage, especially in hot climates.When pipes are stacked under high load pressures and exposed to elevated temperatures, they can sag and lose their perfectly circular shape.
This sagging results in an oval cross-section, which creates inconsistent gaps between the pipe and fitting during EF welding. These gaps compromise the heat distribution, heat transfer, ultimately reducing the strength and durability of the weld.
What Are Flat Spots?
Flat spots, or chords, on pipes are a completely different issue, primarily caused by manufacturing defects. These occur when the pipe is not adequately cooled after leaving the calibrator. The still-soft pipe deforms under its weight when it hits the first roller of the conveyor. This leads to a flat section at the "6 o’clock position" of the pipe.
Flat spots can also develop if pipes are not supported properly during cooling, further increasing the risk of deformation. These flat spots are 100%manufacturing defects and are unrelated to handling, storage, or environmental factors.
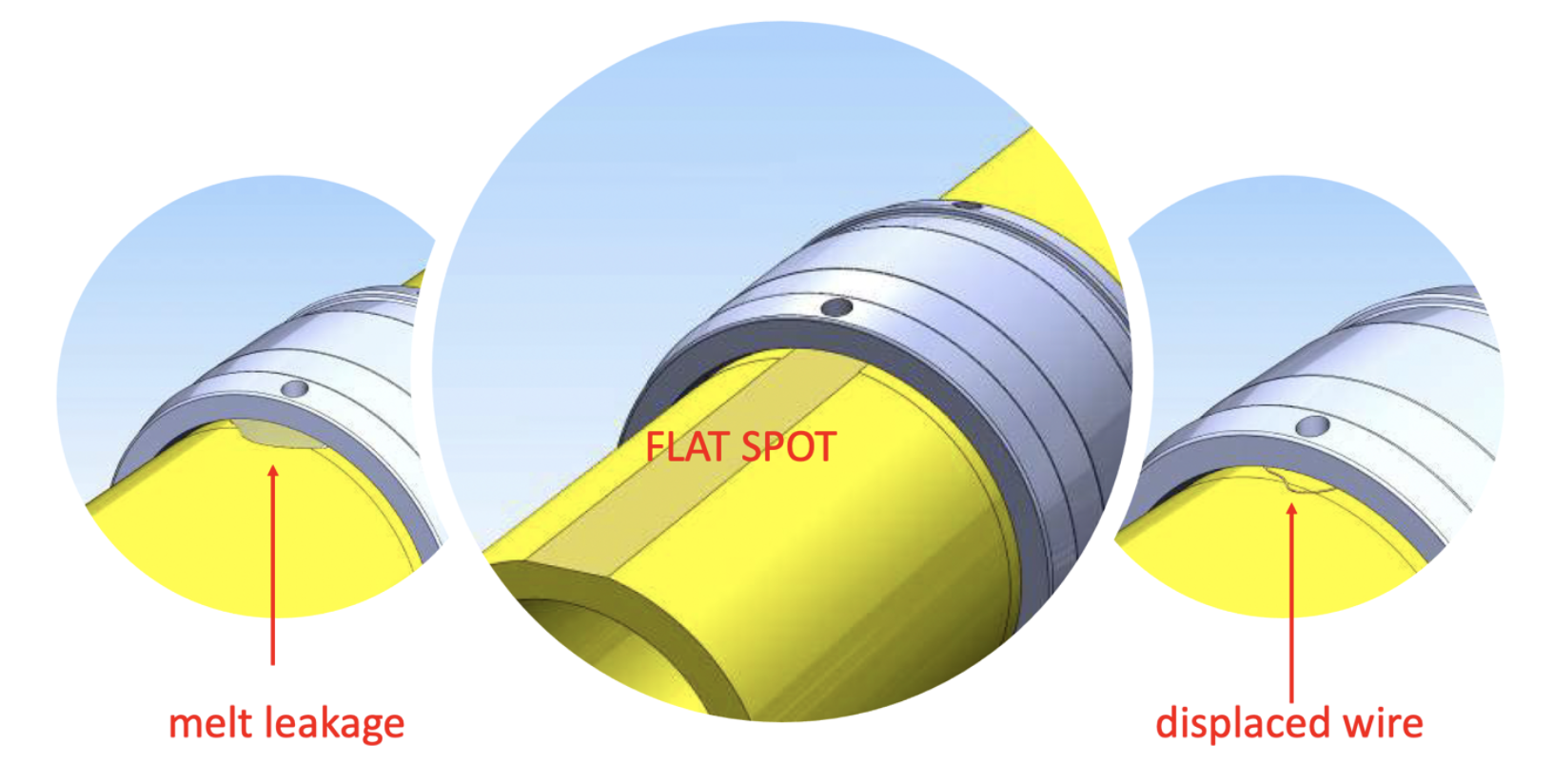
Why Flat Spots Spell Disaster for HDPE Pipe EF Welding
Flat spots pose a critical threat to EF welding. Unlike ovality, which can sometimes be adjusted or corrected by re-rounding tools, flat spots are structural deformations that are nearly impossible to work around. Here’s why:
1. Poor Peeling and Oxidation Layer Removal: Rotary peeling tools are designed to remove the oxidised layer from the pipe's surface before welding. However, when a flat spot is present, the peeling tool "lifts off,"skipping the flat section entirely. This leaves behind oxidised and contaminated material, which prevents proper fusion.
2. Increased Weld Failures: The unpeeled flat spot becomes a weak point in the weld. EF welds require a perfectly clean and uniform surface for proper fusion. Any contamination from the flat spot leads to compromised weld integrity and an increased likelihood of failure.
3. Difficult to Detect: Flat spots are often hard to identify visually. Using tools like pipe ovality gauges is essential to measure circumference and detect these defects. Flat spots cause large gaps between the pipe and fitting, which further hinder the welding process.
4. EF Weld Defects: Flat spots can cause defects in the EF weld such as melt leakage and displaced wires (see figure above courtesy of PPI).
Preventing EF Weld Failures
To minimise the risks associated with flat spots and ovality:
- Reject Pipes with Flat Spots: As per the PE Electrofusion WeldingProcess Checklists, pipes with measurable flat spots must be rejected outright. Even flat spots with a depth of less than 3mm but greater than 1mm can cause significant issues.
- Proper Storage Practices: Avoid storing pipes in hot climates or under heavy loads to reduce ovality risks.
- Check for Defects: Use ovality gauges and other tools to assess pipe roundness and identify flat spots early.
- Demand Accountability: Don’t let manufacturers shift blame to poor handling or transportation. Flat spots are entirely a result of inadequate cooling during production and hence are manufacturing defects.
The Bottom Line
Flat spots and ovality may seem like minor imperfections, but their impact onEF welding can be catastrophic. While ovality is often preventable with properstorage, flat spots remain a manufacturing defect that should never beoverlooked. By thoroughly inspecting pipes and adhering to strict weldingguidelines, you can ensure strong, reliable EF welds and avoid costly failures.