Failure Analysis of Protective Coatings
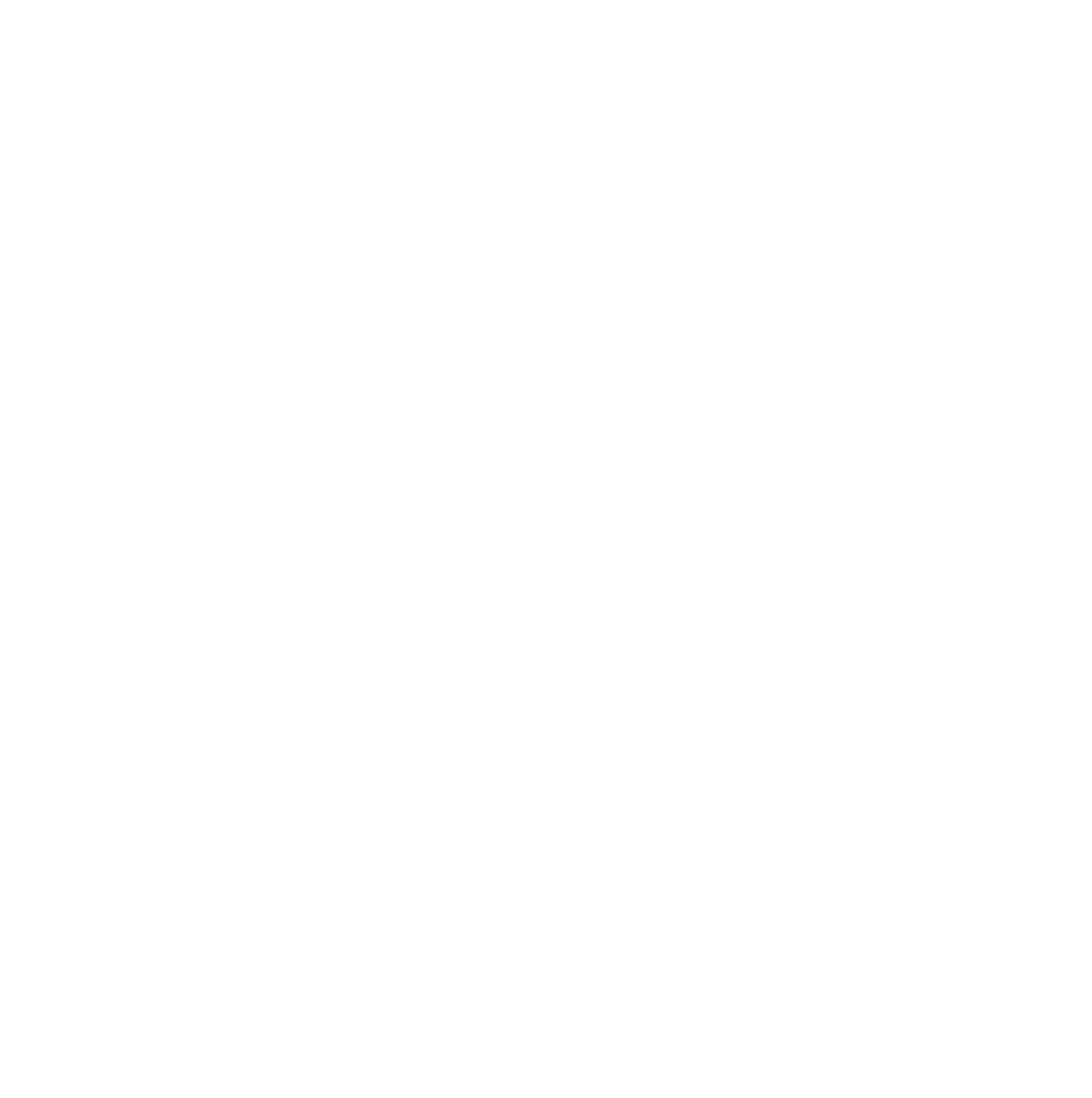
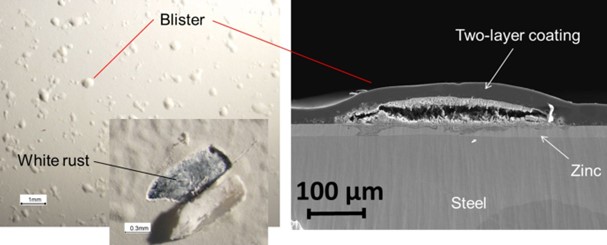
Introduction
Protective coatings are fundamental to preserving the structural integrity of metal assets exposed to aggressive environments. From bridges and ships to storage tanks and transport components, coatings serve as a frontline defence against corrosion,mechanical damage, and chemical attack. However, when these coatings fail, the consequences can be severe- leading to costly repairs, safety risks, and operational downtime.
Why Coatings Fail: A Systems-Level Perspective
Coating failures often manifest as blistering, delamination, cracking, or discoloration, but these symptoms are merely the surface of deeper systemic issues. Effective failure analysis requires a multidisciplinary approach combining materials chemistry, mechanical engineering, and environmental analysis.
A classic example is the constant repainting of steel bridges in marine environments. Previously, frequent maintenance was required due to flaking and corrosion undercutting. Today, innovations such as epoxy glass-flake coatings provide enhanced durability, reducing repainting intervals from every few years to 25 years or more. These advancements underscore the importance of proper coating specification and formulation.
The Stakes in Marine and Industrial Settings
In the maritime industry, coating failures are not just cosmetic—they can trigger insurance claims and costly dry dock periods. Structural repainting or failure remediation, particularly in inaccessible or submerged components, can be logistically complex and economically disruptive. Thus, prevention through correct application, surface preparation, and compatibility with the operational environment is paramount.
Mechanisms of Coating Failure
1. Blistering Due to Osmotic Effects
One of the mos tcommon failures in polymer coatings is blistering. This can arise when semi-permeable coating layers allow water to migrate inward, dissolving water-soluble components (e.g., putty fillers or residual salts) trapped beneath the coating. This establishes an osmotic gradient, driving furtherwater ingress and generating pressure beneath the coating—eventually forming osmotic blisters.
A real-worldcase involved transportation structures painted and wrapped in plastic film for shipping. Moisture ingress during transit caused water to accumulate under the wrapping, and subsequent analysis using Fourier Transform Infrared Spectroscopy(FTIR) and Scanning Electron Microscopy (SEM) identified the presence of chelating agents within the blister fluid. These hydrophilic additives likely contributed to osmotic blister formation, indicating improper pre-coating material control.
2. Surface Contamination and Poor Preparation
Another frequent cause of failure is improper surface preparation. In a case involving palm oil storage tanks, newly applied coatings failed, while older coatings in identical service conditions remained intact. Analytical testing confirmed that the coatings were chemically identical; the failure was traced to surface contamination and inadequate cleaning prior to recoating. Moisture and oils trapped beneath the film catalyzed corrosion, undermining adhesion and allowing coating detachment.
This highlights the critical role of substrate cleanliness and anchor profiling prior to coating application. Inadequate surface prep not only reduces adhesion but may also prevent full curing or crosslinking in reactive coatings such as epoxies and polyurethanes.
Understanding Coating Systems
Every coating system is a combination of four key components:
- Binders (resins): determine film formation and mechanical properties.
- Pigments: add colour and opacity, sometimes corrosion resistance
- Solvents: aid application, later evaporate.
- Additives: modify flow, UV resistance, or chemical resistance.
A formulation optimized for steel corrosion protection may not be suitable for wood,composites, or plastics. Coatings cannot simultaneously be hard and flexible, glossy and matte, or chemically inert and reactive. Material engineers must align coating selection with service conditions, substrate material, and exposure environments.
Analytical Tools in Failure Diagnosis
Failure analysis relies on a suite of laboratory methods:
- SEM/EDX: Morphological and elemental analysis of coating interfaces.
- FTIR: Identification of organic functional groups and degradation products.
- Differential Scanning Calorimetry (DSC): Evaluates curing and thermal stability.
- Adhesion and cross-hatch tests: Assesses mechanical integrity.
These techniques allow identification of failure modes such as underfilm corrosion, poor inter-coat adhesion, chemical attack, and UV degradation.
Some of the coating defects leading to fail are shown in the graphic below.
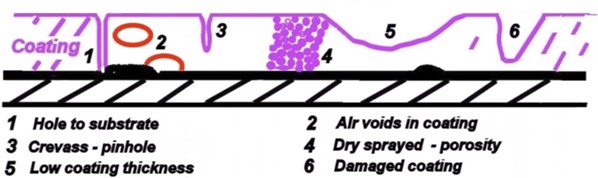
Key Takeaways for Materials Engineers
1. Correct Specification Is Crucial: Understand the service environment and select coatings accordingly.
2. Surface Prep Is Non-Negotiable: Even the best coating will fail if applied to an unclean or improperly profiled surface.
3. Beware of Hidden Interactions: Soluble species in underlayers or from adjacent materials can trigger failures like blistering.
4. Use Failureas a Diagnostic Tool: Each failure is an opportunity to refine system design and prevent recurrence.
Conclusions
Coating failure analysis is more than troubleshooting—it's an exercise in systems engineering. By integrating materials science with field experience and analytical chemistry, engineers cannot only diagnose failures but also engineer resilience into the next generation of protective systems.
Ensure the longevity and integrity of your assets !
With our expert failure analysis services. Our team uses advanced diagnostic tools and a multidisciplinary approach to identify and resolve coating issues before they lead to costly repairs and downtime. Don't wait for failures to happen—proactively protect your investments. Contact us today about your coatings!