Development of Smart Electrofusion Fittings for HDPE Pipe
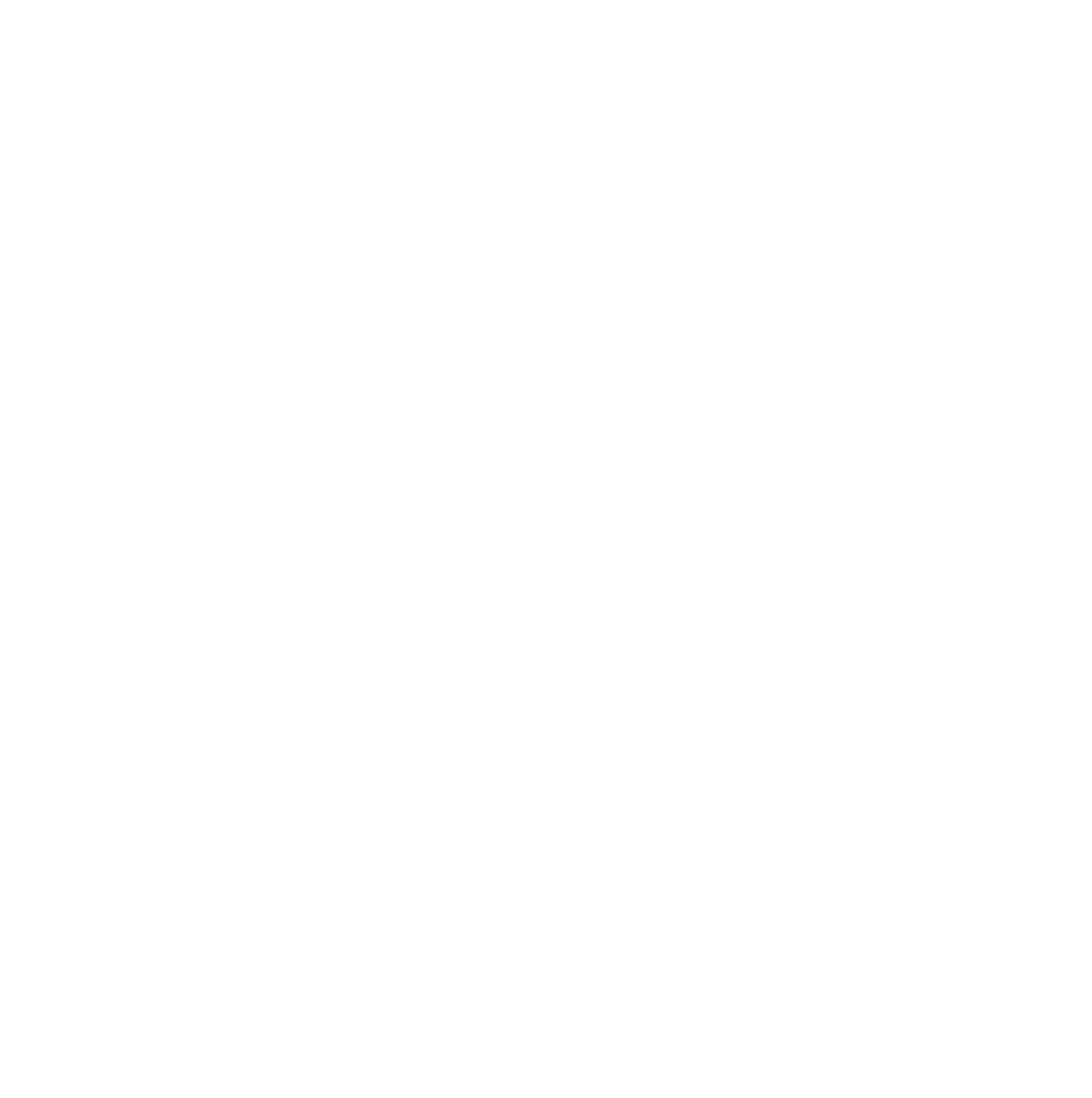
By PPN Editor21st April 2024
Electrofusion (EF) fittings or couplers have long been a staple in the realm ofjoining High-Density Polyethylene (HDPE) pipes, offering a reliable andefficient method for creating strong, leak-proof connections. However, with theadvent of new technologies, manufacturers are now pushing the boundaries ofinnovation by developing smart EF fittings equipped with advanced sensing andreporting capabilities.
Development of Smart Electrofusion Fittings for HDPE Pipe
This article delves into some research and development that major EFmanufacturers are undertaking to produce the next generation of EF fittings.
EF coupler fittings already have electrical contacts so incorporation ofelectronics into the fitting is easily done.
Traditionally EF fittings have two pins that pop out when the correct fusionpressure is achieved hence signalling a completed weld. These pin typeindicators are very simple and do not always work as intended.
Next generation EF couplers may have LED light strips showing the degree ofwelding. They also contain internal sensors to ensure correct assembly andalignment of the pipe with the fitting. This is critical as misalignment stress canresult in electrofusion heating wires moving out of place during the weldingcycle, resulting in overheating and uncontrolled melt flow at the joint inner orouter cold zone.
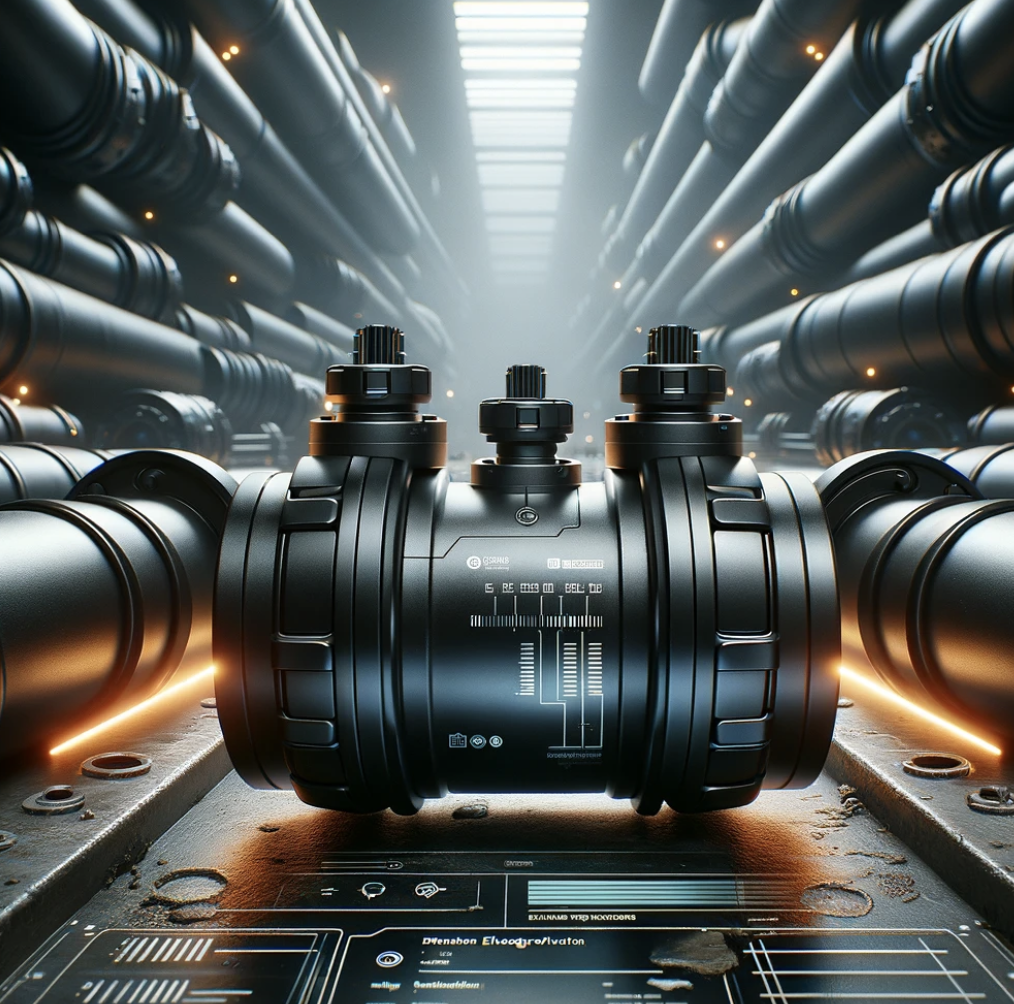
Some new EF fittings under development also have internal infra-red sensors todetect carbonyl products which are a signature of the presence of an oxidizedlayer. In order to achieve an acceptable weld, the oxidised surface of the pipemust first be removed, to expose clean virgin material beneath the surface. Ifsurface oxidation is detected by the fitting it will report it to the ElectrofusionControl Unit (ECU) and that will signal to the operator that removal of thisoxidised surface layer be done with a mechanical peeling tool.
Surface oxidation acts as a physical barrier, inhibiting heat fusion, thereforeconsistent peeling to the correct depth is critical to the success of the weldingprocess, and the only effective means of achieving this is use of a mechanical orrotational peeling tool.
These new generation EF fittings are designed to reduce human error problemssince the effectiveness of current EF jointing depends on attention topreparation of the jointing surfaces and the geometry of the assembly, inparticular the removal of the oxidised surface of the pipe over the socket depthor saddle mounting area, ensuring the jointing surfaces are clean and free fromcontamination, and the assembly and alignment instructions are correctlyfollowed.
Other smart EF fittings have the ability to measure and report strain on the jointfor structural health monitoring of the pipework as shown in the figure below.
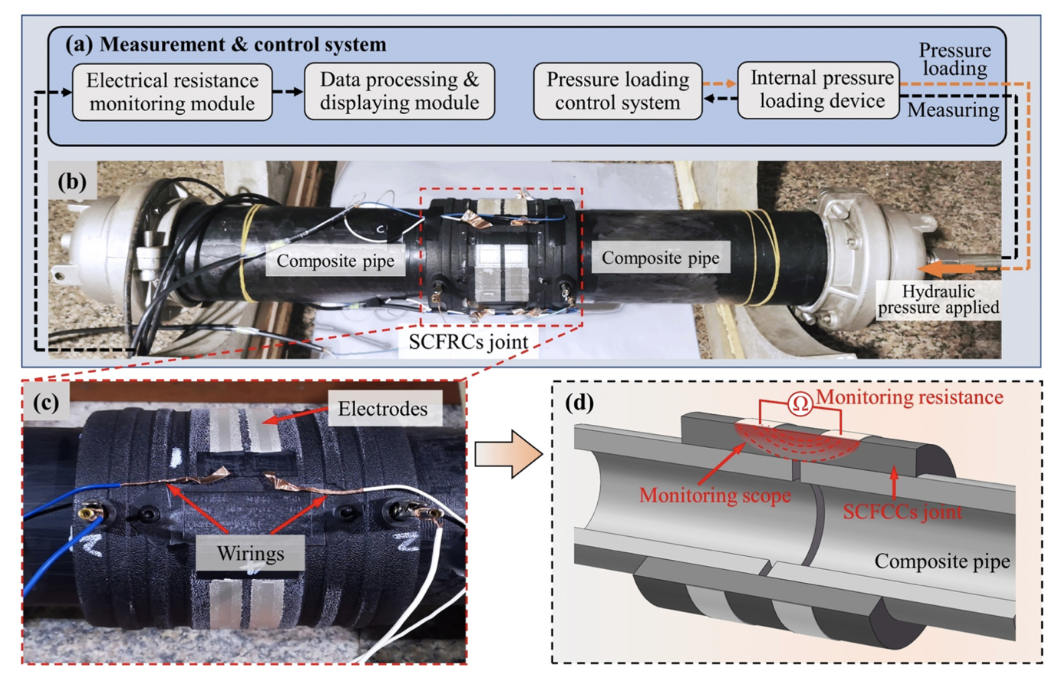
These smart strain-sensing EF fitting are made from HDPE compounded withShort Carbon Fibres (SCF) as shown in the process below. The network ofinterpenetrating carbon fibres can sense strain via a resistance measurement.
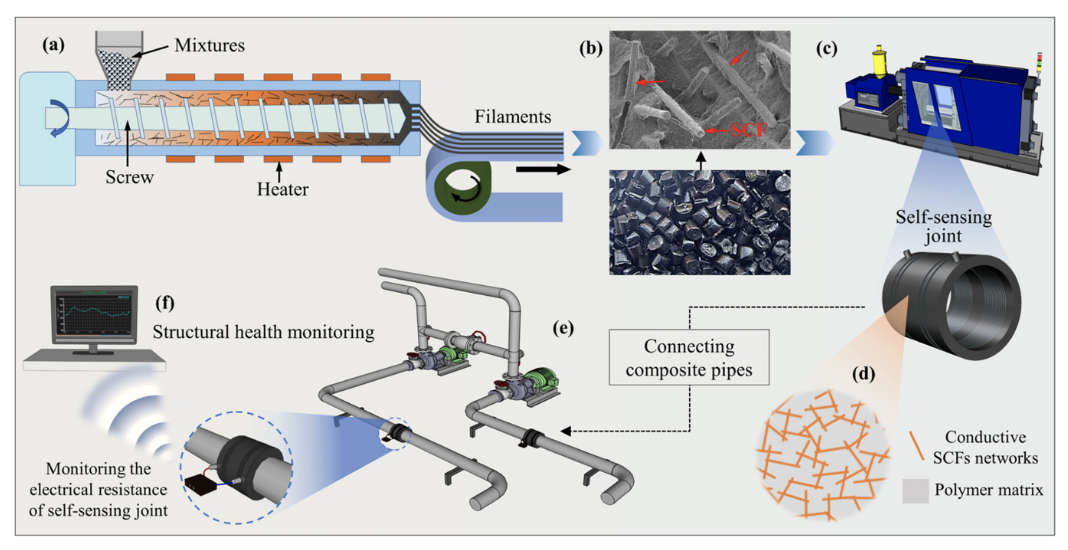
Conclusions
One of the key advancements in smart EF fittings is the incorporation ofelectronic components directly into the fitting. With electrical contacts alreadypresent in EF coupler fittings, integrating electronics becomes a seamlessprocess. These electronics enable the fitting to monitor crucial parameters suchas temperature and dwell time during the welding process, ensuring optimalfusion conditions are achieved.
A notable improvement in the new EF fittings is the introduction of LED lightstrips to provide real-time feedback on the degree of welding. This visualindication allows operators to assess the quality of the joint quickly andaccurately. Additionally, internal sensors are integrated into the fittings to verifyproper assembly and alignment of the pipe, mitigating the risk of misalignment-induced stress that can compromise weld integrity.
Moreover, smart EF fittings are equipped with infrared sensors capable ofdetecting carbonyl products, which indicate the presence of an oxidized layer onthe pipe surface. Surface oxidation poses a significant challenge to the weldingprocess as it inhibits heat fusion, leading to weak joints and potential leaks.Upon detecting oxidation, the fitting communicates with the ElectrofusionControl Unit (ECU) to alert the operator to remove the oxidized layer using amechanical peeling tool. This proactive approach ensures that only clean, virginmaterial is fused, thereby improving joint strength and reliability.
The introduction of smart technology in EF fittings marks a significantadvancement in the field of HDPE pipe joining. By reducing reliance on manualinspection and intervention, these fittings minimize the risk of human error andenhance the consistency and quality of welded joints. Furthermore, theystreamline the welding process, saving time and labour costs while improvingoverall system performance by sensing strain in service.
In conclusion, the development of smart electrofusion fittings represents apromising step forward in the evolution of HDPE pipe joining technology. Withtheir advanced sensing and reporting capabilities, these fittings offer improvedaccuracy, reliability, and efficiency, paving the way for safer and more robustpipeline installations in various applications.