HDPE Pipe Resin Manufacturers Embrace Non-PFAS Polymer Processing Aids Amidst Growing Regulatory Pressure
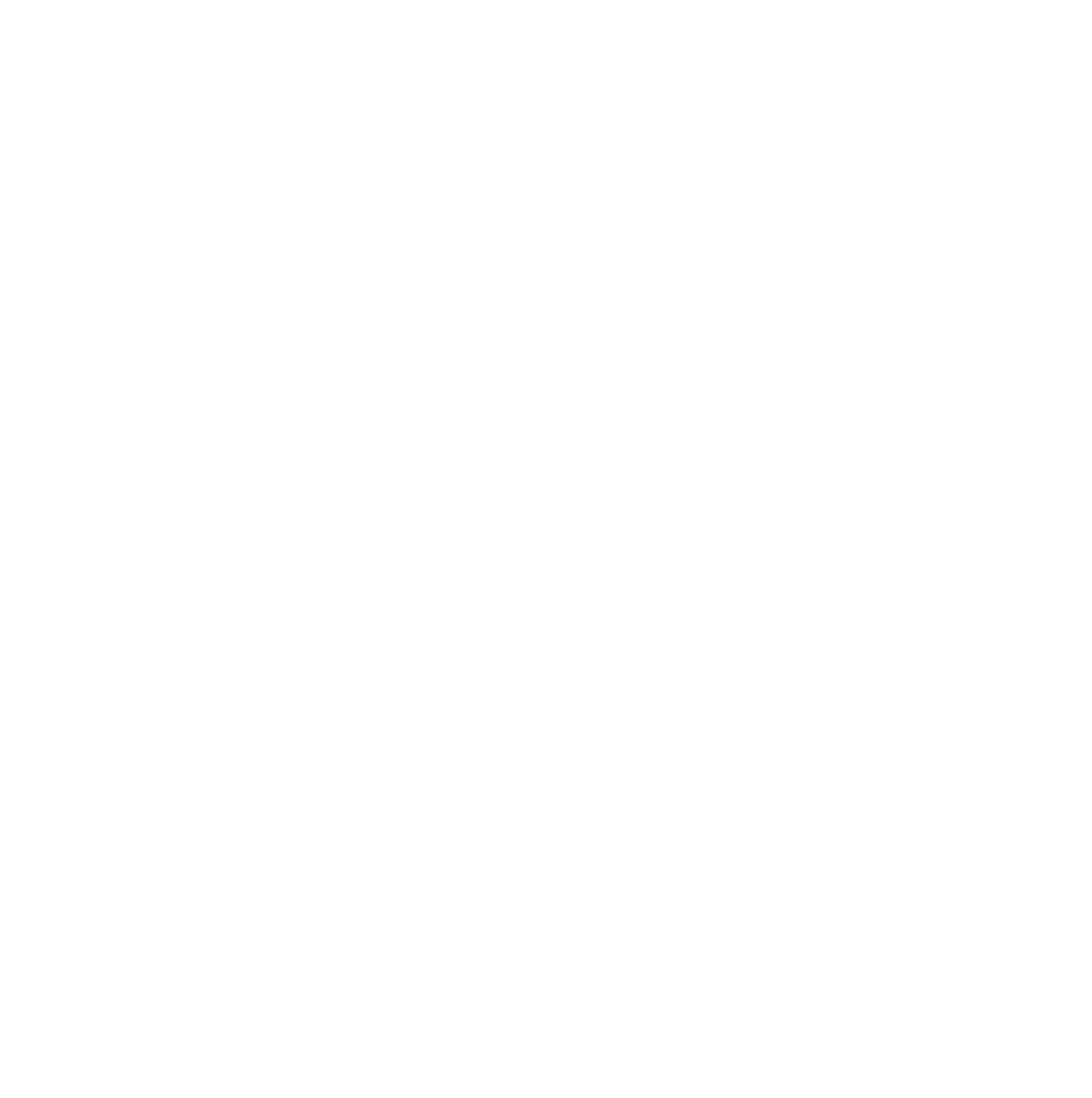
By PPN Editor
Introduction
High-Density Polyethylene (HDPE) pipes play a crucial role in water and gas conveyance industries and in civil engineering projects. These pipes are manufactured using high-molecular weight polyethylene resins, with the aid of polymer processing aids (PPAs) to enhance production efficiency. Furthermore the advent of low-sag HDPE resins with even higher melt viscosity necessitate the use of PPAs.
Traditionally, fluorinated polymers mixed with fluorosurfactants have been the go-to PPAs due to their ability to reduce melt fracture, pressure, process temperature, and machine torque, resulting in higher output rates. However, recent European legislation and growing regulatory concerns have prompted HDPE pipe resin manufacturers to transition towards non-PFAS alternatives.
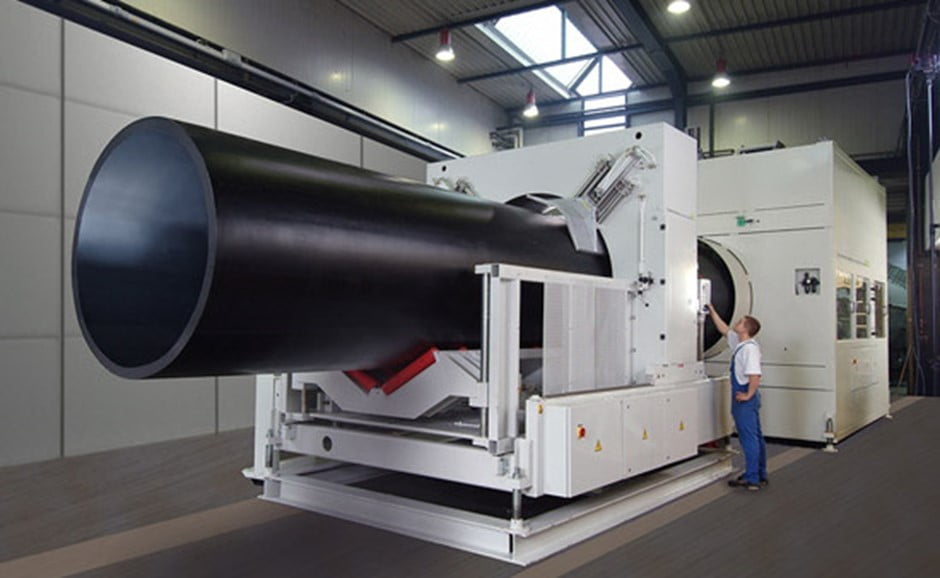
The Benefits of Polymer Processing Aids (PPAs) in HDPE
Polymer Processing Aids (PPAs) have long been integral to HDPE pipe production. These additives offer significant advantages, including:
- Increased Extrusion Speed: PPAs enable manufacturers to boost extrusion speed without the need to raise processing temperatures. This not only enhances production rates but also lowers energy consumption.
- Smooth Surface Finish: PPAs help achieve smoother surface finishes, eliminating melt fracture that can otherwise occur during extrusion. This not only improves product quality but also reduces production costs.
Challenges and Regulatory Pressures
As the HDPE pipe industry faces increasing regulatory scrutiny, particularly in Europe, there is a growing shift away from PFAS-regulated PPAs. In February 2023, the European Chemicals Agency proposed a ban on per- and polyfluoroalkyl substances (PFAS), including PFAS-containing PPAs. Member states are set to vote on this ban in 2025, potentially phasing out exceptions for fluorinated chemicals over the next 7-12 years.In the United States, the Environmental Protection Agency is working towards implementing mandatory drinking-water limits on PFAS compounds. Many U.S. states have already imposed restrictions on PFAS usage across various applications, including polymer processing aids for HDPE pipes.
The Exit of Major PPA Producer
In December 2022, a major producer of fluorinated PPAs, 3M, announced its decision to exit the entire fluoropolymer business by 2025. This decision was motivated by increasingly stringent regulations and customer demand for PFAS alternatives. The withdrawal of a major player from the PFAS market has raised concerns about the availability of PPAs and the potential for legal challenges.
The PFAS Classification Dilemma
Legislation and regulatory activities in both the U.S. and the European Union have proposed classifying fluoroelastomers as PFAS compounds. This broad classification encompasses a wide range of substances, including well-known contaminants like PFOA and PFOS, as well as fluoroelastomers with strong evidence supporting their non-toxicity. Research indicates that fluoroelastomers are non-bioavailable, non-toxic, non-mobile, do not dissolve in water, and do not degrade into other PFAS forms. Despite their benign environmental and toxicological profiles, they are currently categorized as PFAS.
Supply Chain Challenges
The supply of fluoroelastomers for polymer processing aids is already constrained by a tight supply chain. The regulatory uncertainty surrounding PFAS compounds has created confusion and ambiguity in the marketplace. Manufacturers are re-evaluating their capital capacity increases, and some, like 3M, have chosen to exit the fluoropolymer business due to market uncertainty, a lack of viable alternatives, and potential litigation.
Emerging Non-PFAS Alternatives
The supply of fluoroelastomers for polymer processing aids is already constrained by a tight supply chain. The regulatory uncertainty surrounding PFAS compounds has created confusion and ambiguity in the marketplace. Manufacturers are re-evaluating their capital capacity increases, and some, like 3M, have chosen to exit the fluoropolymer business due to market uncertainty, a lack of viable alternatives, and potential litigation.
Conclusions
As the HDPE pipe industry grapples with heightened regulatory scrutiny, manufacturers are adapting to evolving environmental standards by seeking non-PFAS alternatives for polymer processing aids.The proposed bans on PFAS compounds and the reclassification of fluoroelastomers as PFAS have raised concerns about supply chain stability. However, the industry's resilience is evident in the development of non-PFAS alternatives that maintain performance standards while aligning with increasingly stringent regulations.The transition towards environmentally friendly PPAs represents a significant step in ensuring the sustainability and compliance of HDPE pipe production in the face of growing regulatory pressure in the PFAS space.