Harnessing the Benefits of AI in Geosynthetics Installation
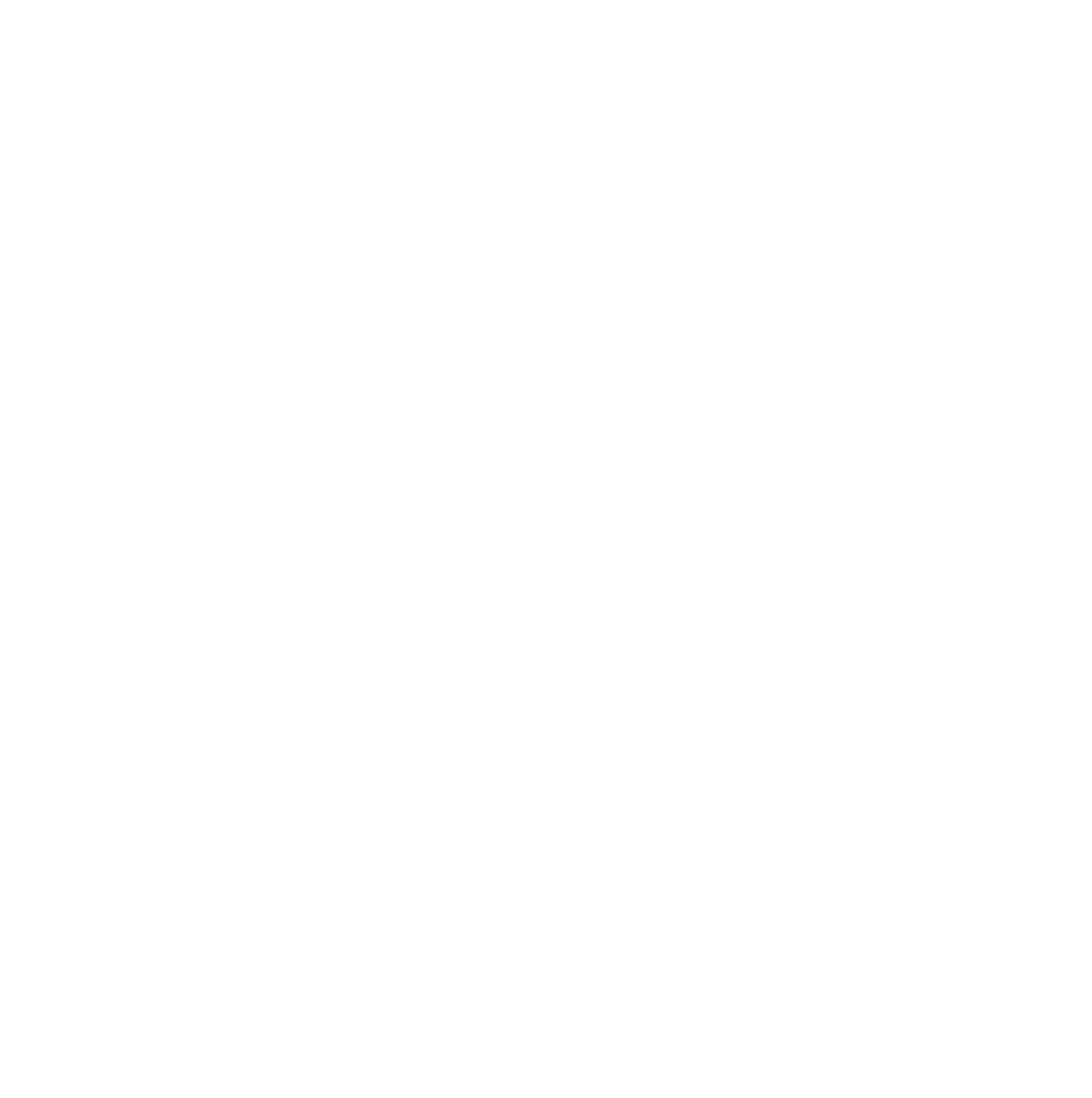
Authors
J. Scheirs and A. Marta1. Director, ExcelPlas, Melbourne, VIC, Email: john@excelplas.com.au2. Senior Principal | Director, Red Earth Engineering a Geosyntec Company, Brisbane,QLD, 4000, Email: attila@redearthengineering.com.au
In Cooperation With
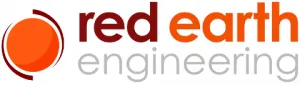

Introduction
As the geosynthetic installation sector attempts to manage current global challenges, it is beginning to rely on AI technology and sensor technology to ease some pressure. This white paper explains what AI technology is and outlines the business case for investing in this technology.For installers of geosynthetic new AI technology can ease some of the pressure, especially regarding labour shortages, maintenance, and data analytics. AI technology is proving to be vital in the growth of the geosynthetics industry as it offers productivity, efficiency, and cost savings.Artificial intelligence (AI) is a modern reality that is transforming industrial operations and outcomes. Due to recent advances in edge AI technologies – which combine edge computing and AI – organisations can start unlocking value now from huge amounts of sensor and operational data. This informs decision-making to optimise operations and reduce costs. It also enables automation, which drastically improves the safety and efficiency of processes.In a nutshell, it is the way of the future, and geosynthetic installers that take advantage of edge AI now will have a competitive advantage. Those who stall on the adoption of these technologies run the risk of losing their ability to compete effectively.
What is Edge AI?
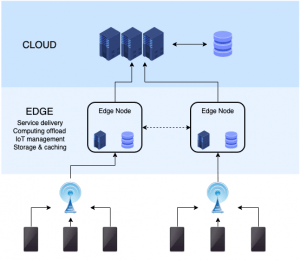
Edge AI is a marriage of edge computing and AI. To understand how the pairing works, it’s important to first comprehend the concept of edge computing and its advantages. Edge computing relates to its location, on the edge. It is a type of network infrastructure that facilitates data processing and storage at or near the source of data generation. Typical sources of data are Internet of Things (IoT) devices such as sensors that are attached to equipment. Due to the sheer amount of data collected from IoT devices in real time, traditional computing architecture – which relies on a centralised data network – isn’t suitable to processing, analysing, or storing this ever-growing ocean of data at speed.How does edge AI work?
AI has the ability to train and learn with human-like capability. AI algorithms can understand language and interpret sensory information such as sights, smells, and touch. Which is why they are helpful in places where end users are and real-world problems exist. However, to perform human-like tasks, AI technology relies on the computation of complex machine learning algorithms and rapid data transmission. This creates challenges around bandwidth, latency and privacy.
Edge computing makes industrial scale AI feasible. Because with edge AI, the AI is working via machine learning algorithms located and stored locally. How does it do this? AI uses what is called a deep neural network (DNN) to replicate human intelligence. In a process referred to as ‘deep learning’, the DNN is trained to respond to numerous question types whilst it is connected to a centralised data centre or cloud to access the data required.
Once the training is complete, the AI model graduates to becoming an ‘inference engine’. This means it can be deployed on the edge, where it can successfully run off a localised computer or device to perform tasks based on its existing knowledge. When it runs into a problem, it uploads the problematic data to the cloud for further training of the original model, which in turn replaces the inference engine. Simply put, the edge AI model continues to get smarter.
A great example of using edge AI is with predictive maintenance. When combining the use of IoT sensors with AI, anomalies in geosynthetic materials or equipment such as welders can be detected early and used to predict when the machine or componentry will fail. This allows installation businesses to optimise their maintenance and avoid costly downtime.With edge AI, these sensor-enabled devices can collect and process data locally without having to communicate with the cloud, meaning decisions are made quickly and with real-time insights. By processing the data on site through sensor-enabled devices, installers also avoid any potential network disruptions that could interrupt their installation schedules or processes.
For installers of geosynthetics relying on edge AI technology this can ease some pressure, especially regarding labour shortages, maintenance, and data analytics. AI technology is proving to be vital in the growth of the geosynthetics industry as it offers productivity, efficiency, and cost savings.
Some practical example of the use of AI are to correlate the geomembrane welder settings such as wedge temperature, nip pressure and speed to the final performance of the geomembrane welds such as shear and peel strength of the welds.
Another good example is the valuable correlation that can be calculated by AI between the short-term Strain Hardening Method (SHM) tests to determine stress crack resistance (SCR) and the long-term Notched Constant Tensile Load (NCTL) testing for SCR that can take many weeks to complete in the case of the latter.A great example of using edge AI is with predictive maintenance. When combining the use of IoT sensors with AI, anomalies in geosynthetic materials or equipment such as welders can be detected early and used to predict when the machine or heater componentry will fail. This allows installation businesses to optimise their maintenance and avoid costly downtime. With edge AI, these sensor-enabled devices can collect and process data locally without having to communicate with the cloud, meaning decisions are made quickly and with real-time insights. By processing the data on site through sensor-enabled devices, installers also avoid any potential network disruptions that could interrupt their installation schedules or processes.
Use of Advanced Sensors to Track Geomembrane Performance and Life
Setting up and monitoring of geomembrane lined assets require a clear understanding of the complexities of the combination of in-service factors such as UV, temperature, pH, stress, which can only be achieved with advanced sensors.
With many geomembrane-lined assets located in remote areas, and unprecedented rainfall and floods (i.e., changing weather patterns) it is difficult to understand the full extent of geomembrane ageing when site access becomes an issue.
Collecting data from multiple types of sensors as well as predictive modelling can reduce uncertainty and inform decision-making as to the remaining life of geomembranes. The future of data technology in geosynthetics will combine various sensors and modelling to understand what is really happening to liner systems.
There are four new ways for assest owners/operators and regulatory bodies to understand in-service geomembrane conditions and performance:
- AI integration and modelling
- Low-cost telemetry sensors
- In-situ condition monitoring sensors
- Drones and Satellites.
To better understand the condition of geomembrane-lined assets one can use a combination of low-cost physical sensors and remote sensors. These sensors are able to gather data at a lower cost and are easy to install. Paired with remote sensors, strategically placed telemetry sensors can provide better insight into the current state and performance of geomembranes.
Recently the development of optical-fibre sensors and the methods to incorporate the sensors within geomembranes during manufacture provides mainstream access to sensor-enable geomembranes and other geosynthetics. Such systems are being developed to monitor the effects of strain on geomembranes including the location of tears.
Other possible measurements utilize moisture and fluid-level sensors. Since the use of geomembranes in geotechnical and environmental applications is widespread and monitoring systems are generally lacking, the potential for this technology is significant. For example, a geomembrane-and-sensor system addresses the need to monitor landfill stabilization in general and specifically the behaviour of geomembranes used in liner and cover designs.
Glass and polymer optical fibres can be attached to geomembranes by different means for example: (1) during extrusion and lamination and (2) by hot shoe welding, glued tape runners, and welded runners. One preliminary focus has been on strain sensors to monitor landfill settlement. Geomembranes have been produced utilizing existing and newly developed strain sensors, e.g., microbend, Bragg grating, and adsorption band sensors. These sensors have been installed as arrays into several test geomembranes at a manufacturing scale (e.g., 3 to 4 m wide). The sensors measure the strains across the geomembranes as they are loaded.Over the years, due to advantages over traditional transducers (e.g., strain gauges, inclinometers), including high precision and online monitoring, fibre optic sensing technology has been developed for monitoring internal deformation in geo-structures. In recent years, a new geosynthetic material called sensor-enabled geogrid was developed by integrating the fibre Bragg grating (FBG) sensors into the geogrid for real-time monitoring.
A newer approach utilizes flexible conductive material such as graphene masterbatches. Graphene master batches have superior qualities such as good electrical conductivity, structural flexibility, high chemical and thermal stability, lightweight, and potential mass production, enabling them to be promising candidate materials for sensor-enabled geosynthetics.
Conclusions
AI technology has emerged as a critical tool for the geosynthetic installation sector in managing current business challenges. The use of edge AI technology in particular offers practical solutions for labour shortages, maintenance, and data analytics, leading to improved productivity, efficiency, and cost savings.Through AI, correlations can be made between various factors such as welder settings and final weld performance, carbon black content and stabilizer effectiveness, and short-term SHM tests and long-term NCTL testing for SCR.
Additionally, the combination of IoT sensors and AI enables predictive maintenance, allowing for the early detection of anomalies in geosynthetic materials or equipment and the optimization of maintenance schedules to avoid costly downtime.
With edge AI processing data locally, decisions can be made quickly and with real-time insights, while also avoiding potential network disruptions. Ultimately, the integration of AI technology will prove to be a vital contributor to the growth and success of the geosynthetics industry.
The use of advanced sensors is essential to monitor and understand the complexities of geomembrane performance, including in-service factors such as UV, temperature, pH, and stress. With many geomembrane-lined assets located in remote areas and unpredictable weather patterns, gathering data from a combination of sensors and predictive modelling is necessary to reduce uncertainty and inform decision-making regarding the remaining life of geomembranes.
The future of data technology in geosynthetics will combine various sensors and modelling techniques, such as AI modelling, low-cost telemetry sensors, quantum sensors, drones and satellites, and groundwater recharge, to understand what is happening to liner systems. Recently, optical-fibre sensors have been developed and incorporated into geomembranes during manufacture, providing mainstream access to sensor-enabled geosynthetics.
This technology has significant potential in monitoring landfill stabilization and the behaviour of geomembranes used in liner and cover designs. Newer approaches, such as theuse of graphene masterbatches, show promise in creating sensor-enabled geosynthetics with superior qualities.