Geosynthetic Inputs and Manufacturing– Properties that impact Product Life not captured in Technical Datasheets
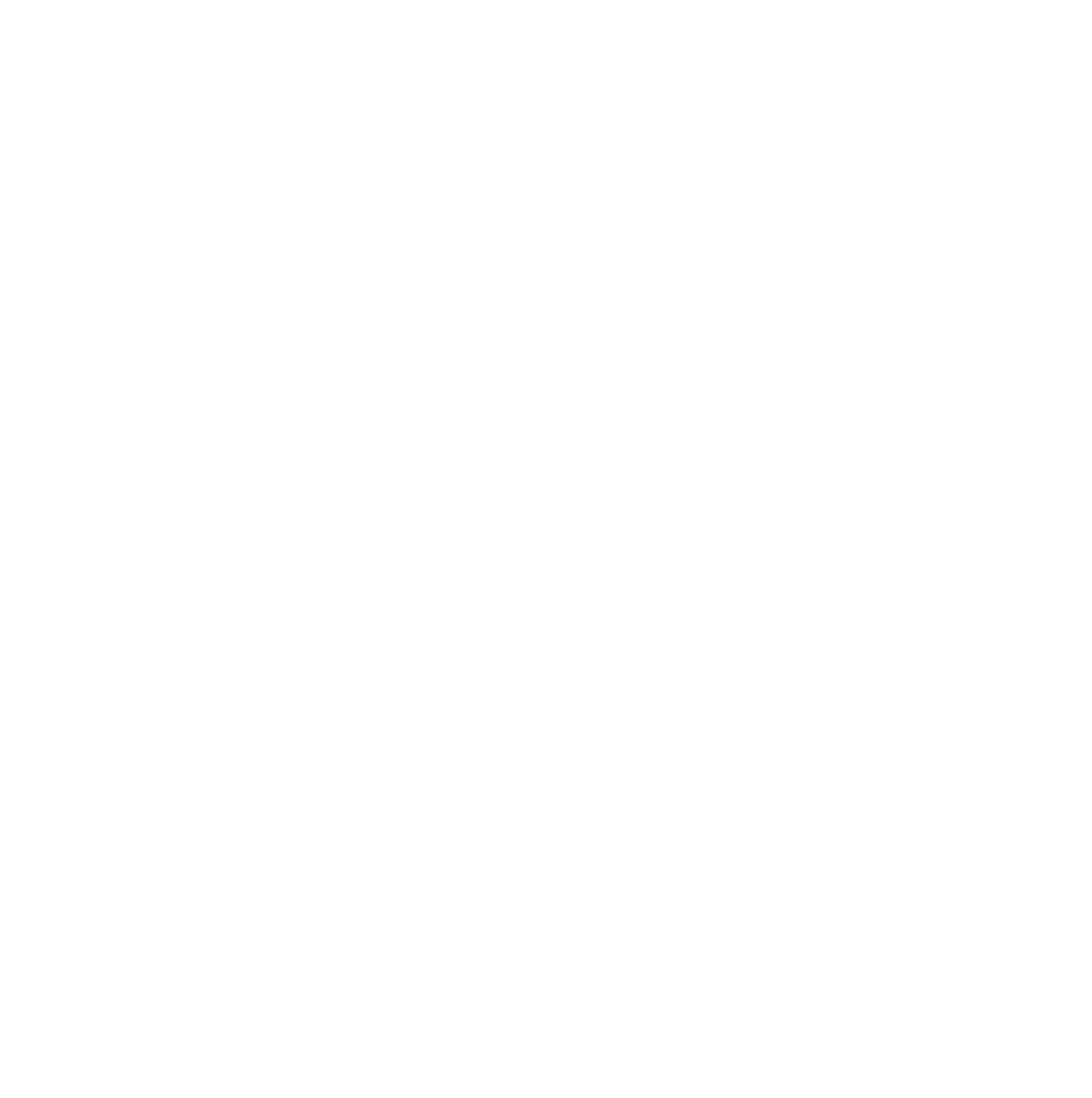
By GNA Editor
Opinion Pieces by Marc Amtsberg (Atarfil) and John Scheirs (ExcelPlas)
Marc has spent 20 years of working in the Geosynthetic sector as both a client and working with major manufacturers and he has observed an ongoing challenge across the industry. Marc has found that remains a general lack of focus on both the Geosynthetic Inputs and Manufacturing Processes that are so critical to product design life.
John has been testing polymers and geosynthetics for 30 years and he has pioneered some of the industry’s latest testing to evaluate long-term durability such as deformulation testing of additives in geosynthetics, thin-film accelerated immersion testing and the use of strain hardening modulus as a surrogate for the NCTL stress cracking resistance test.
An evaluation of the raw material and manufacturing process provide the key insight into expected Geosynthetic performance. Yet this is often overlooked in academic studies, in critical project testing, even for projects that require accountability in EPA regulations.
A reputable manufacturer will have extensive data and must be willing to identify their raw material supplier, their quality processes. If not willing to reveal their polymer inputs, demonstrated testing and project history then serious doubts should be raised over the suitability of their materials.
The fundamental challenge in using Geosynthetics, is short term testing on very small samples is being used to make performance assumptions for projects that can be millions of square metres. This assumption is only correct, if the product properties are replicated across every square metre. A designer who invests time to understand product inputs and manufacturing process, is better equipped to understand this project risk.
In this new GNA series, Marc and John document the most common technical questions encountered for common landfill and mining geosynthetic lining systems. Many of these properties are not measured by QC Testing, but nevertheless are critical in determining Geosynthetic product life.
Geotextiles - Polyester or Polypropylene?
Introduction
The choice between polyester (PET) and polypropylene (PP) geotextiles for non-woven cushioning in landfills is a common concern among geosynthetic specialists.
Since the early days of geotextiles, both PET and PP fibres have competed in the manufacturing of nonwoven fabrics. Each resin type has its advantages and disadvantages, with PP gaining popularity due to its lower cost and specific gravity, allowing for more fibres per unit weight. This technical note provides a summary analysis of polyester and polypropylene geotextiles, focusing on their manufacturing processes, properties, long-term performance, and suitability for different environmental conditions.
Polyester Geotextiles
Manufactured through entangling fibres and applying additional thermal treatment, non-woven polyester geotextiles possess inherent UV stability and exhibit resistance to degradation. PET-based geotextiles have demonstrated long-lasting exposed performance, as evidenced by the persistence of PET-based soda bottles in the environment. However, variations in polyester sourced from different suppliers should be considered, and caution is advised in high pH environments such as landfills with alkaline waste or when placed in direct contact with cement/concrete.
Polypropylene Geotextiles
Non-woven polypropylene geotextiles, commonly used in landfill cushioning, are manufactured using similar processes to polyester geotextiles. However, PP geotextiles are highly dependent on additive packages for UV stability and resistance to oxidation. Over time, PP geotextiles tend to degrade when exposed to weathering, leading to a reduction in tensile strength and oxidative embrittlement (see figure below showing embrittlement of UV-exposed PP geotextile).
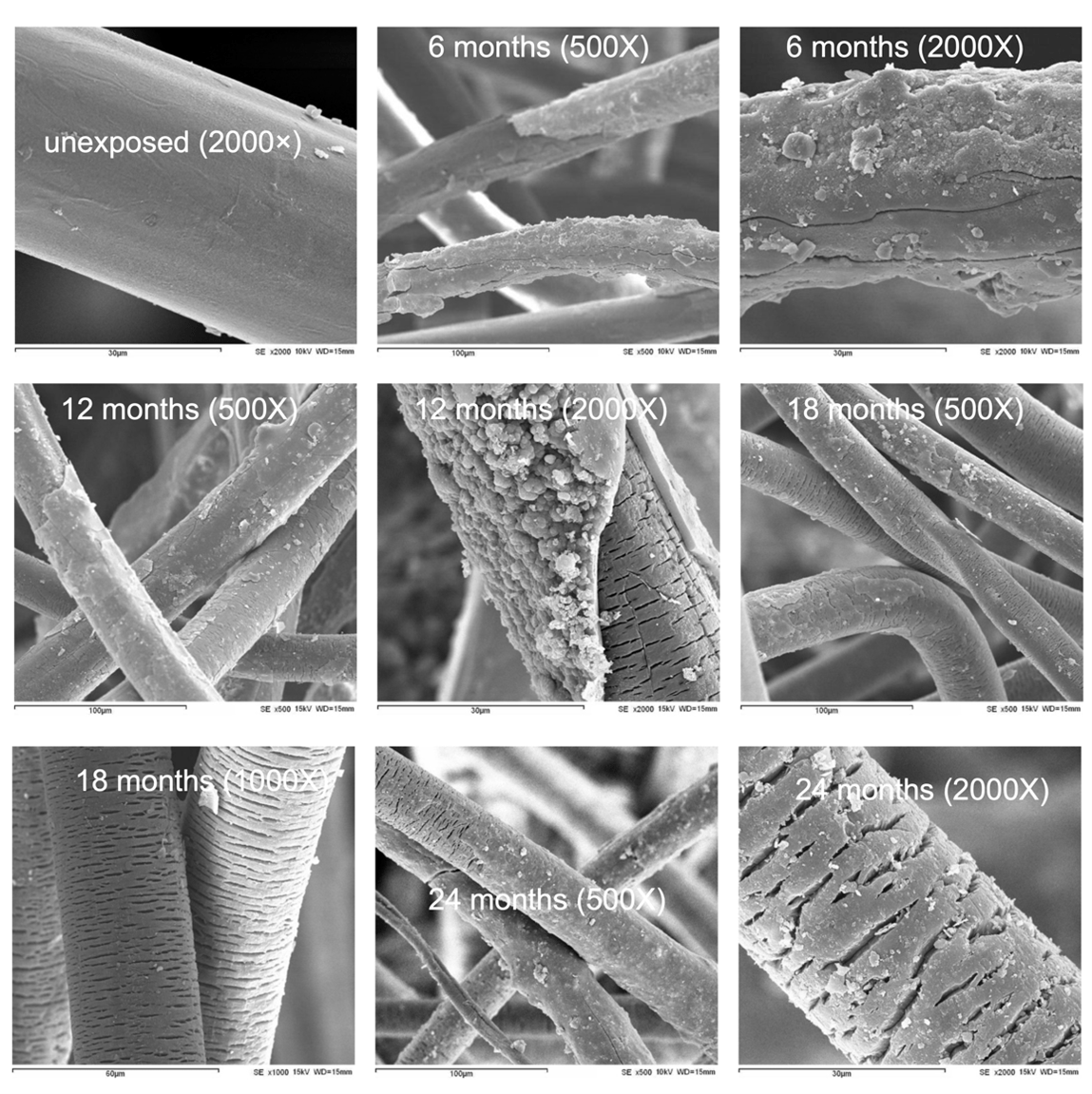
Field tests have shown significant decreases in tensile strength, ranging from 50% to 94% after six to twelve months of exposure. Although well stabilized PP materials exhibit slower degradation, caution is advised when using PP geotextiles in exposed applications, particularly in regions with intense UV radiation due to their susceptibility to photooxidation.
For well stabilised PP geotextile materials, degradation is slower. Reductions in tensile strength ranging from 39 to 82% were reported for three commercial PP geotextiles with different stabilisation packages exposed to natural weathering for 36 months (Carneiro, 2018). In another study a PP geotextile experienced a reduction in tensile strength of 84%, also after 36 months (Aparicio-Ardila, 2021).
Comparative Analysis
Cost and specific gravity are important factors to consider when choosing between polyester and polypropylene geotextiles. While PP geotextiles offer a lower cost and higher fibre density, polyester geotextiles provide better intrinsic UV stability. The choice should also depend on the specific project requirements and the history and testing of the geotextile polymer source. The table below summarizes the respective general advantages and disadvantages of PP and PET geotextiles.
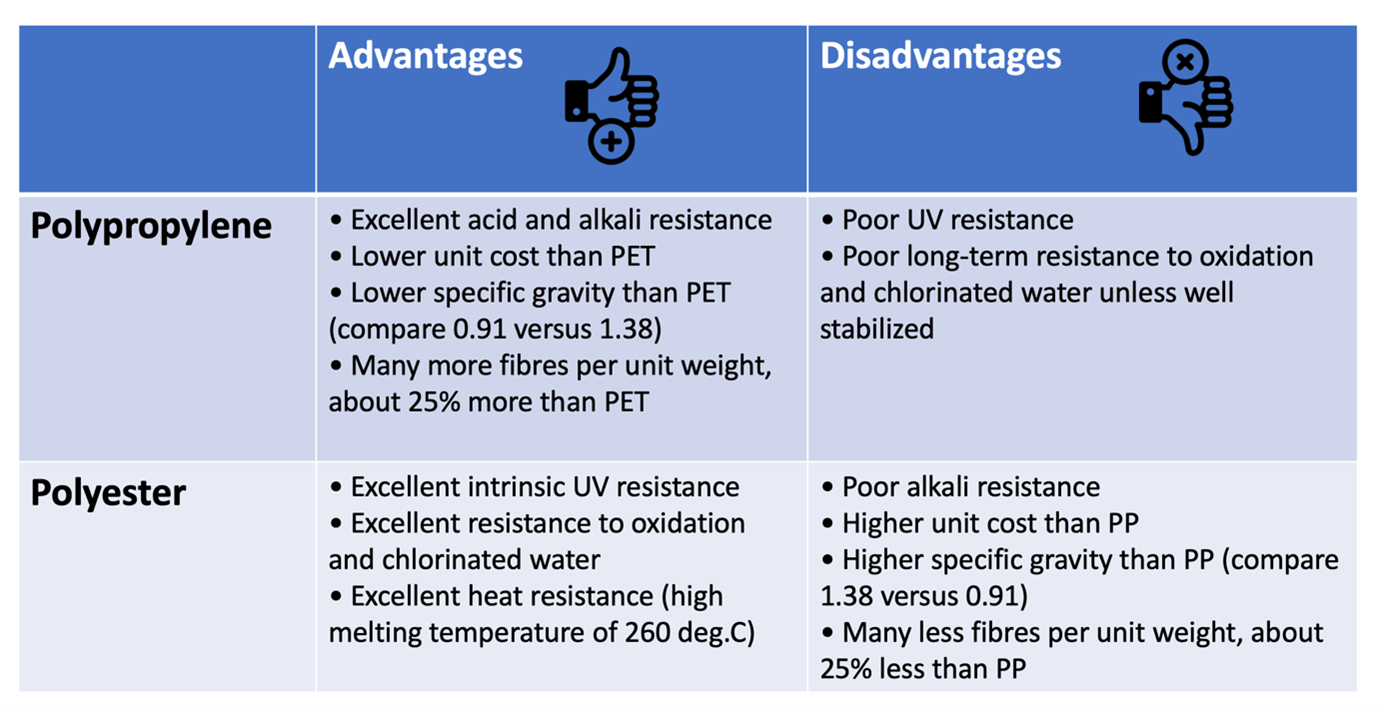
Conclusions
When selecting geotextiles, particularly for critical projects, it is crucial not to rely solely on the polymer category (polyester or polypropylene).
Evaluating the history and testing of a specific geotextile polymer source is essential to ensure long-term design performance. Polyester geotextiles are not recommended for use in high pH environments (e.g. paper pulp dregs, lime waste or red mud) or in direct contact with cement/concrete. Caution should be exercised when using polypropylene geotextiles in exposed applications, especially in regions with intense UV radiation.
By considering the characteristics, limitations, and suitability of polyester and polypropylene geotextiles, engineers and geosynthetic specialists can make informed decisions regarding the choice of geotextile material for landfill cushioning and other applications.
Do not rely solely on a polymer category alone, evaluate the history and test a specific geotextile polymer source on critical projects.
References and More Reading
Carneiro, J.R.; Lopes, M.L. Natural weathering of polypropylene geotextiles treated with different chemical stabilisers. Geosynth. Int. 2017, 24, 544–553.
Carneiro, J.R.; Morais, M.; Lopes, M.L. Degradation of polypropylene geotextiles with different chemical stabilisations in marine environments. Constr. Build. Mater. 2018, 165, 877–886.
Aparicio-Ardila, M.A.; Pedroso, G.O.M.; Kobelnik, M.; Valentin, C.A.; Luz, M.P.; Silva, J.F. Evaluating the degradation of a nonwoven polypropylene geotextile exposed to natural weathering for 3 years. Int. J. of Geosynth. Ground Eng. 2021, 7, 69.