Failure Analysis Report of HDPE Water Pipe
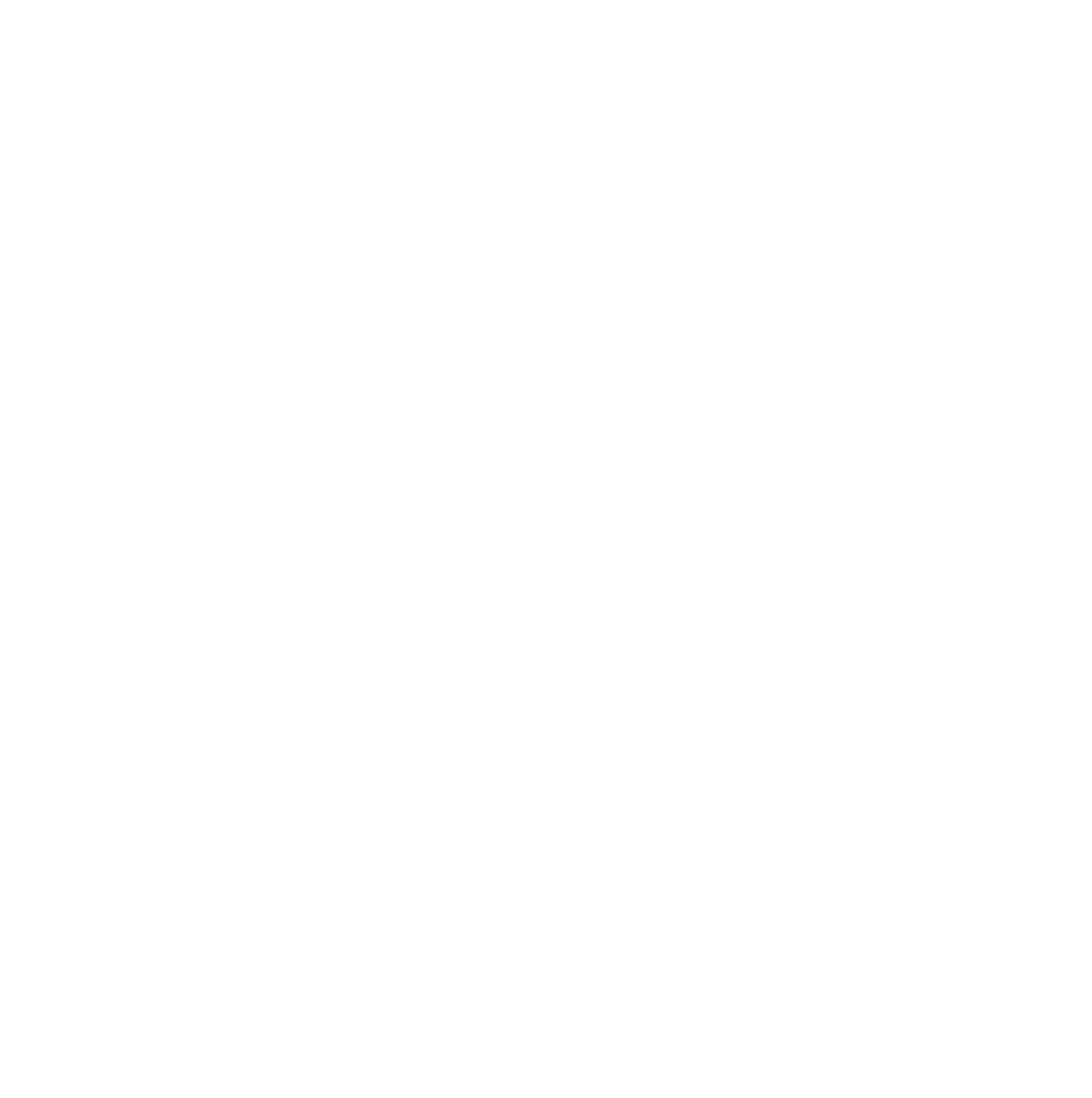
Objective
To investigate cracking of a High-Density Polyethylene (HDPE) pipe.
Testing Undertaken
- Physical testing methods, such as strain-induced Bend Back testing
- Microscopy examination / Fractography
- S-OIT
ExcelPlas polymer testing Laboratory located in Melbourne, Australia investigates material product failures such as cracking of a High-Density Polyethylene (HDPE) pipe. This was conducted through physical testing methods such as strain-induced Bend Back testing and Microscopy examination / Fractography as well as analytical tests including oxidation induction time (S-OIT), and Carbonyl Index. The observed crack propagation mechanism is evident in the below figures.
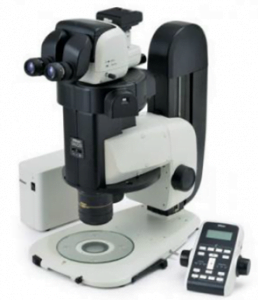
Stereomicroscopy (Microcracking)
Microcracking on dead fold was assessed using a Nikon SMZ25 stereographic optical microscopy (SOM).Only the exposed side of the samples was subjected to 180 degree ‘dead fold’ and was observed for incipient microcracking at various magnifications.The liner samples were bent back and dead folded (180 degrees) so that the surface of the liner was placed in tension and under strain.The bend back specimens were then placed in restraint clips and the top faces of the fold specimens were microscopically examined for any evidence of microcracking.Whilst the bending stress is somewhat in excess of that likely to be encountered in service it will determine if any incipient micro cracking or brittle layers are present on the liner surface. Quality virgin liner samples subjected to this test do not exhibit any micro cracking.
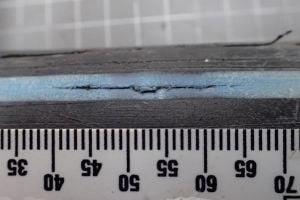
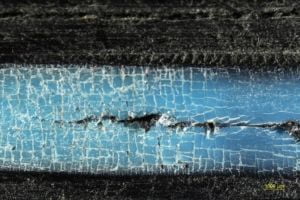
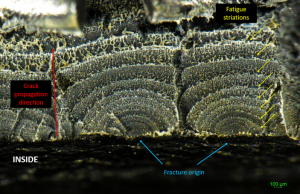
SOIT
Oxidation induction time (OIT) measurements were conducted on the samples to determine residual additive levels. The sampling method for S-OIT included the exposed side of all samples was cleaned with water to remove the built-up dust layer. Thin slices were prepared from the both sides by using a cutting blade. The exposed side of the samples was in contact with the sample pan during OIT testing. No homogenization was carried out prior to sampling.
The HDPE pipe most likely failed by fatigue cracking, initiating at multiple embrittled and degraded areas on the internal pipe surface (which was significantly oxidised). The blue stripe at the 12o’clock position was exposed to UV light before service, and resulted in surface embrittlement and microcracking, however was NOT the primary cause of failure in this case but a secondary contributor to the through-wall cracking at that location as the cracking direction was inside to outside.
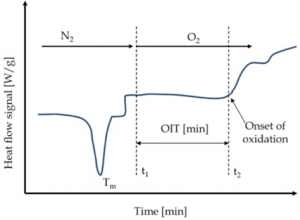
ExcelPlas Laboratories provides a comprehensive plastic pipe testing service and is equipped with a state-of-the-art laboratory to test a range ofpolymeric materials including polyethylene and polypropylene. ExcelPlas can carry out testing on plastictubing and pipe ranging in wall thickness from 3 mm to 80 mm. ExcelPlas Laboratories provide a comprehensive service to Industrial & commercial companies, environmental consultants, Government bodies and local Authority customers throughout Australia & NZ. All testing is carried and out in accordance with ISO & ASTM methods and is fully accredited to ISO 17025 by NATA where relevant. Litigation support on material testing and analysis can also be provided.