Breakdown of Protective Coatings in the LNG Industry
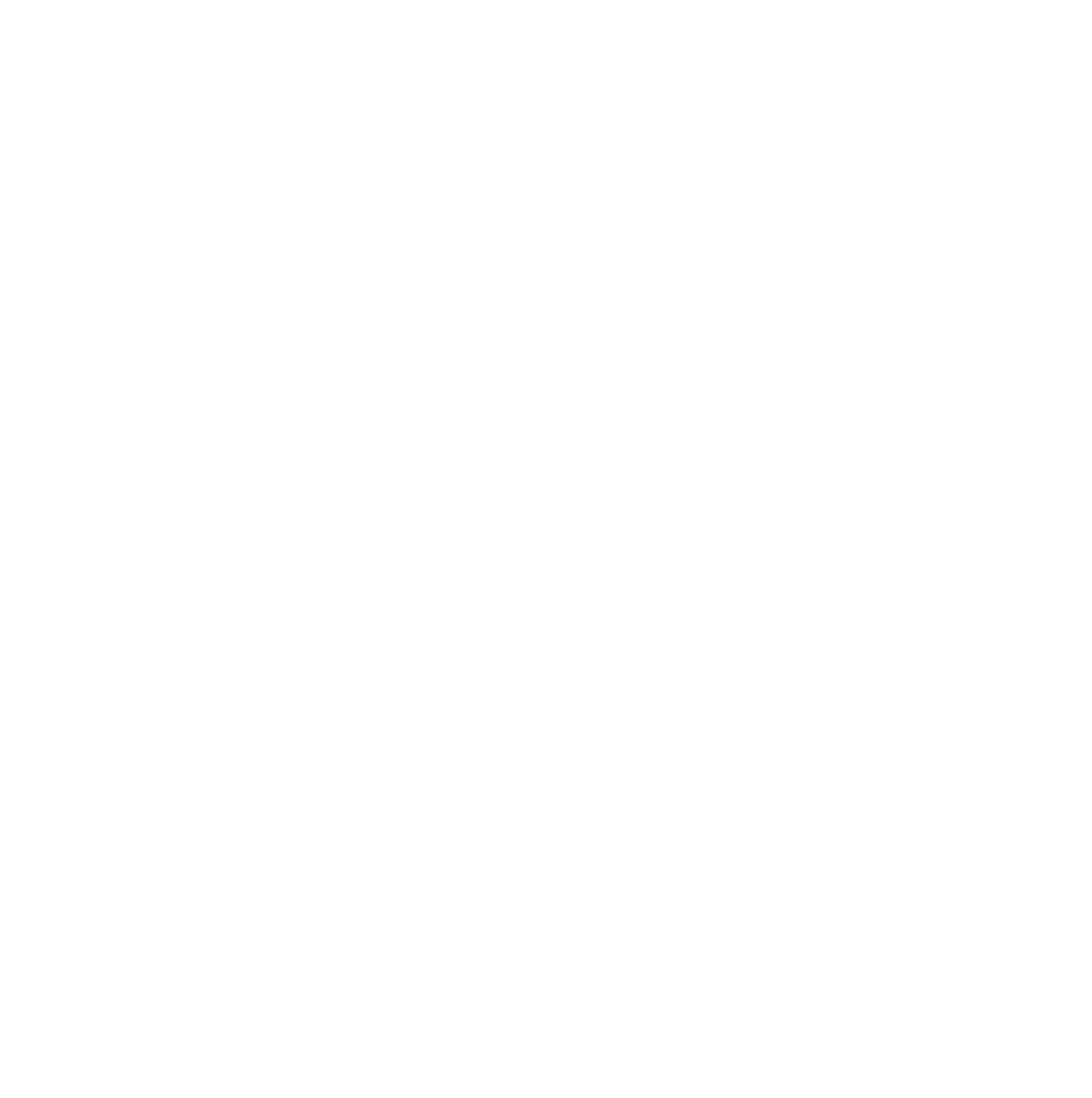
By PCN Editor
To parody a well-known phrase “… Corrosion and events wait for no man! …” King Canute may have sought to command the sea to obey his commands to illustrate this point, but he certainly did not have the rotten impact of ‘corrosion’ in mind.
The phrase does, however, provide an appropriate illustration when reflecting on the pace of development in today’s LNG industry and its concerning impact on the management of the integrity and safety of LNG production, operations, and transport.
It is corrosion that carries the burden of risk for the LNG industry, and thus should provide the focus for corrosion management.
Those with rose-tinted glasses might comment that much of the LNG industry’s corrosion challenge is limited by the degree to which operating atmospheres are cryo-genic or ‘exotic’ in nature. But, outside of these ‘exotic’ atmospheres, protective coatings continue to break down over time impacting vessel/pipe integrity and the integrity of ballast tanks; and corrosion under insulation (CUI) on non-cryogenic lines remains an omnipresent threat.
The degree to which pipes corrode is dependent on a number of factors that include the performance of the metal used in the pipe, the operating pressures and temperatures, and the corrosivity of the material flowing through it.
As an example, a Schedule 80 carbon steel pipe carrying crude oil may have a measured corrosion rate of 2 mm/y and a wall thickness of 11 mm thus, unless measures to reduce the risk are put in place, might experience a perforation and leak within 5.5 years; possibly earlier, where the pipe requires wall thickness for structural integrity as well as pressure containment.
The hidden dangers of corrosion under insulation (CUI) span the oil and gas industry from upstream operations to midstream infrastructure to downstream applications, including the production of liquified natural gas (LNG).Many LNG assets face an elevated risk for corrosion under insulation (CUI) to develop and proliferate.
CUI is a severe form of localized corrosion that occurs when water, inorganic salts and other contaminants become trapped beneath insulation covering pipes, valves, tanks and other assets, leading to the formation of corrosion cells that are hidden from view and can spread unnoticed.In LNG operations, cold/cryogenic temperatures can contribute to increased CUI risks.
Moisture from condensation can be especially prevalent under insulation in cryogenic LNG operations due to the extreme temperature differentials with ambient air. Newer liquid coatings offer facilities the opportunity to mitigate corrosion far longer than previous options, helping owners extend coating maintenance schedules, reduce operational costs and enhance safety.
Protective Coatings: A Solution to Mitigate Corrosion
Newer protective coatings offer facilities the opportunity to mitigate corrosion far longer than previous options, helping owners extend coating maintenance schedules, reduce operational costs, and enhance safety. These advanced coatings are specifically designed to withstand the harsh conditions of the LNG industry, including extreme temperatures and exposure to corrosive substances.Some key benefits of these advanced coatings include:
- Extended Lifespan: These coatings have demonstrated the ability to provide long-lasting protection against corrosion, significantly extending the lifespan of critical assets such as pipes, tanks, and valves.
- Cost Savings: By reducing the frequency of coating maintenance and replacement, LNG facilities can achieve substantial cost savings over the long term. This not only includes the cost of materials and labor but also the potential savings associated with avoiding downtime and repairs due to corrosion-related failures.
- Enhanced Safety: Maintaining the integrity of LNG assets is paramount for safety. Corrosion can weaken structures and lead to leaks or failures that pose significant safety risks. Advanced coatings help ensure the structural integrity of equipment and reduce the likelihood of accidents.
- Environmental Benefits: Corrosion-related leaks can have detrimental environmental consequences. These coatings help prevent such incidents, reducing the risk of environmental contamination and the associated clean-up costs.
- Regulatory Compliance: Meeting regulatory standards is a crucial aspect of LNG operations. Using advanced coatings that are designed to resist corrosion can assist facilities in complying with industry regulations and standards.
In conclusion, corrosion remains a significant challenge in the LNG industry, and the breakdown of protective coatings is a key contributor to this problem.
However, with the development and implementation of advanced liquid coatings designed to withstand the extreme conditions of LNG operations, facilities can effectively mitigate corrosion risks, extend the lifespan of critical assets, reduce operational costs, enhance safety, and ensure compliance with industry regulations.
As the LNG industry continues to evolve, corrosion management and protective coating technologies will play a vital role in maintaining the integrity and safety of its operations.